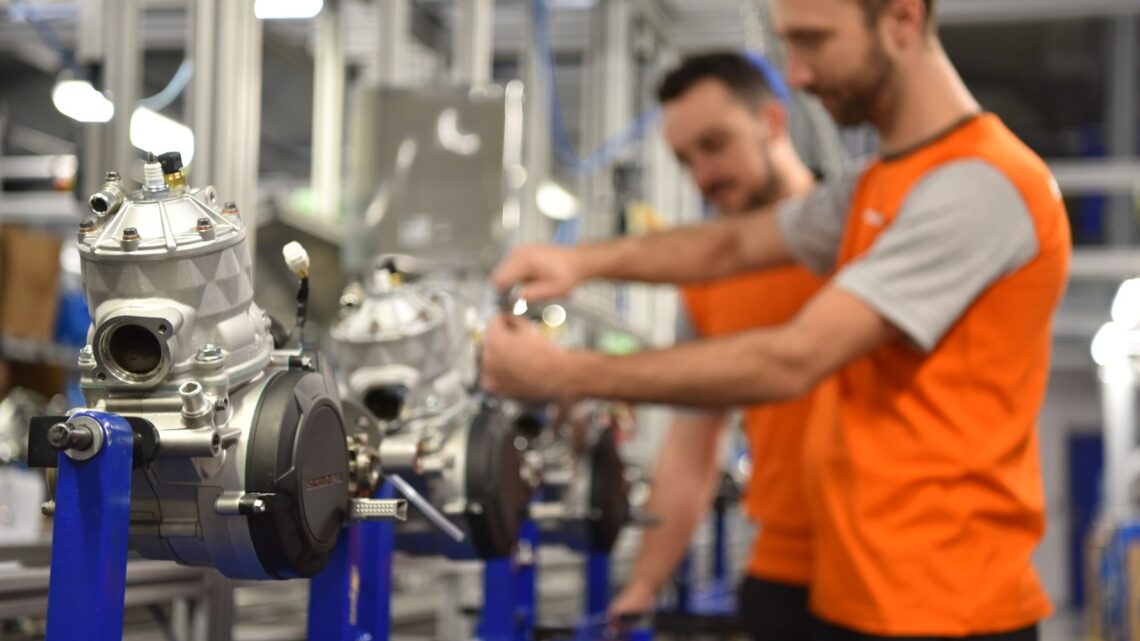
Speciale Infotrial.Visita lo stabilimento Scorpa e Sherco
12 Febbraio 2024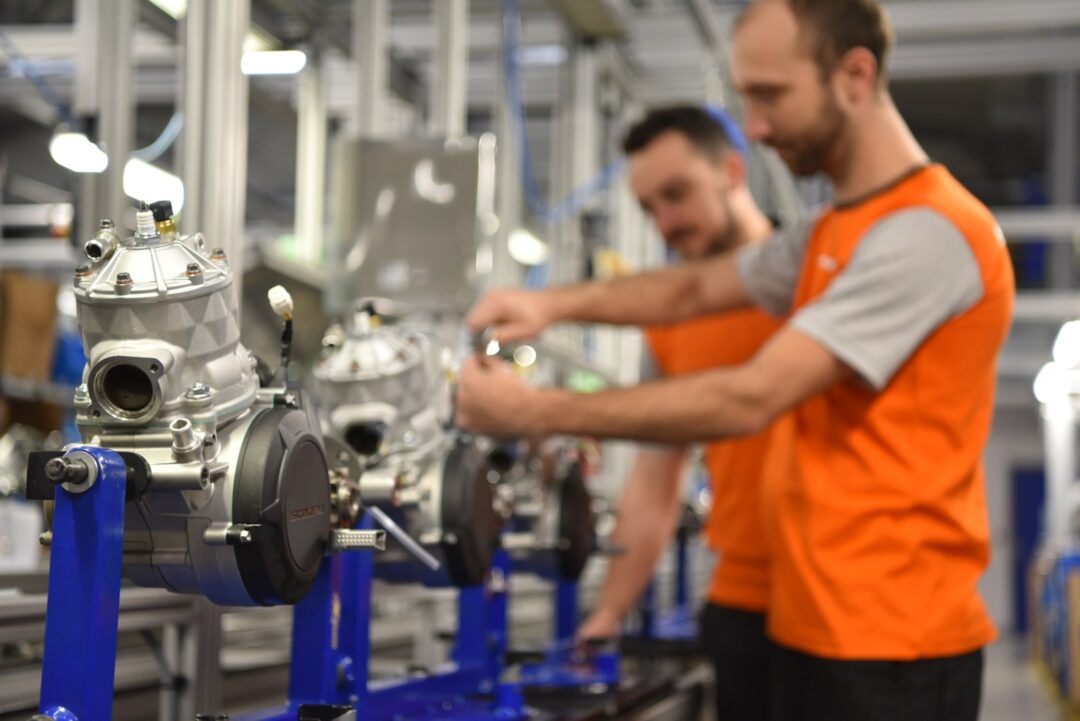
Due marchi nati dalla passione della stessa persona per il trial.
Scorpa e Sherco sono entrambi un progetto di Marc Teissier, imprenditore francese con la passione per il nostro sport.
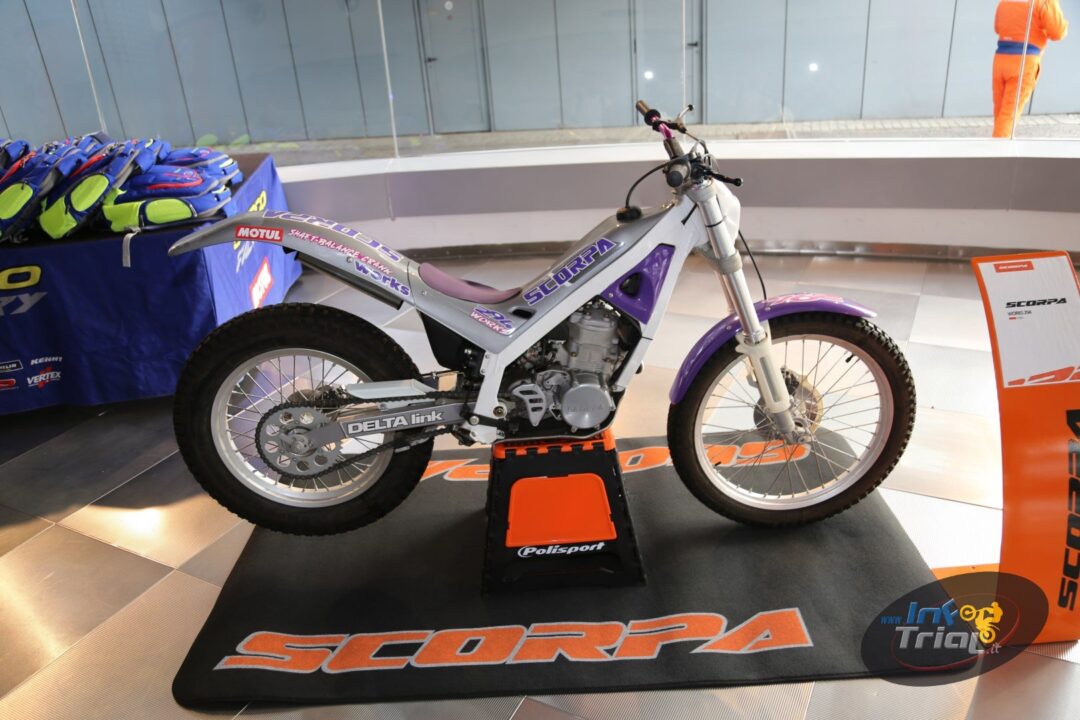
La Prima Scorpa
Era il 1993 quando la Scorpa Works fu lanciata sul mercato, nel 1998, invece, fu la volta della prima Bultaco Sherco.
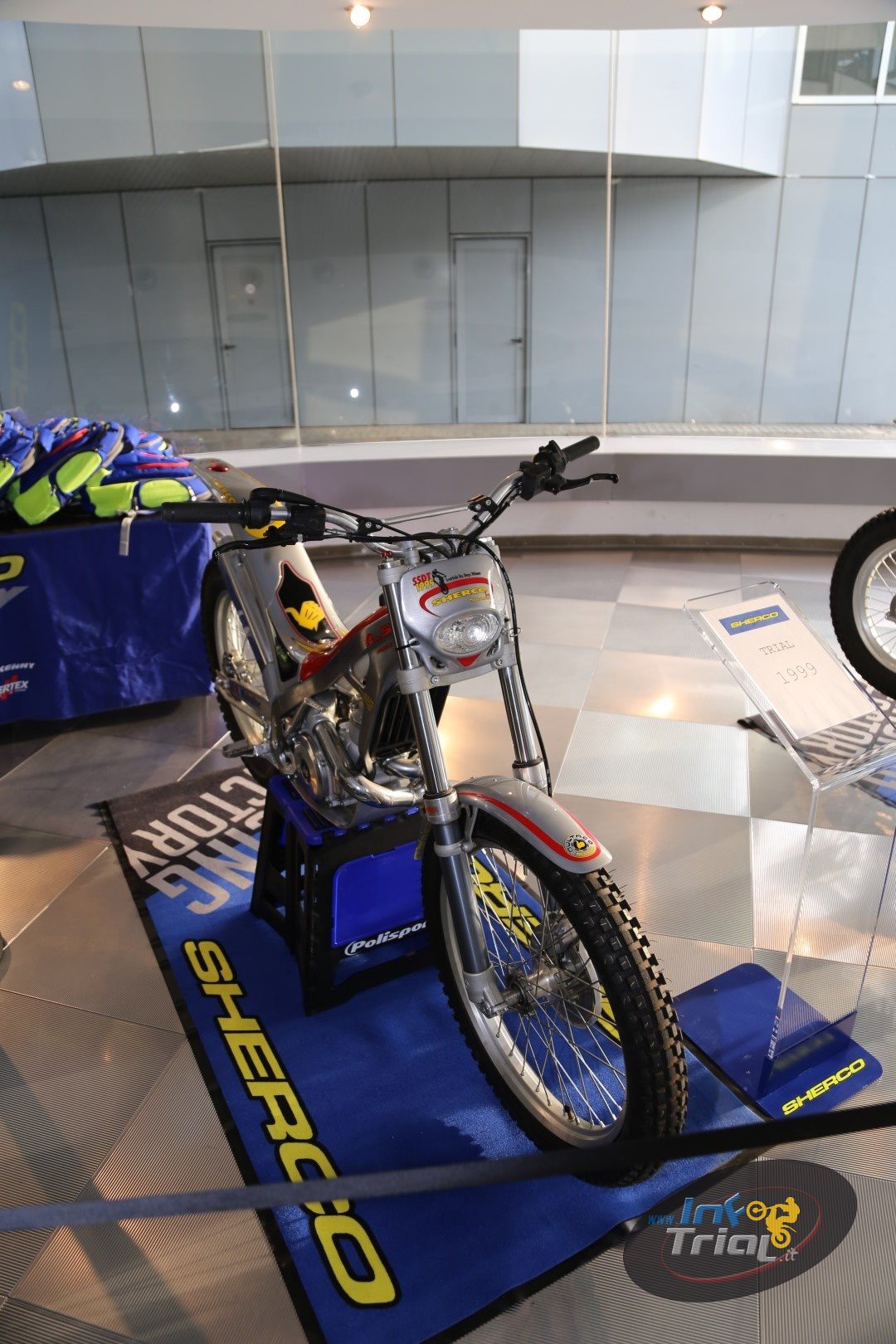
La prima Sherco
Si, il marchio dal pollice alzato ritornò nel trial per una stagione prima da lasciare il posto a quello Sherco.
E mentre sul finire del millennio le due case avevano proprietà diverse, Teissier cedette il marchio ad altri imprenditori, qualche anno dopo Sherco e Scorpa tornarono ad essere controllati dal francese.
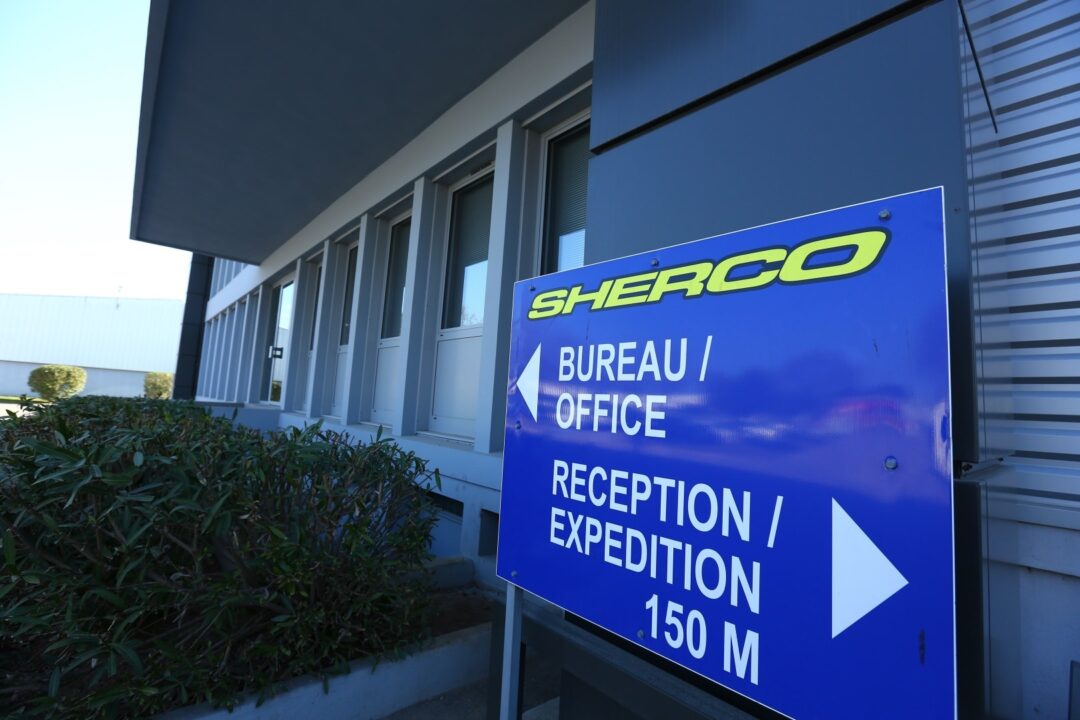
Oggi a Nimes, in un moderno stabilimento costruito 5 anni fa e nel quale gli accessi ai vari reparti produttivi sono regolati da un sistema con chiavi elettroniche, prendono forma le trial franco spagnole.
Si perché il gruppo capitanato da Teissier vede due siti produttivi a Nimes ed un terzo, in Spagna nel quale vengono montate le ruote e la gamma E-bike.
In Francia sono 170 i dipendenti impiegati nei due siti produttivi e a guidarci nella visita è stato Didier Tirard.
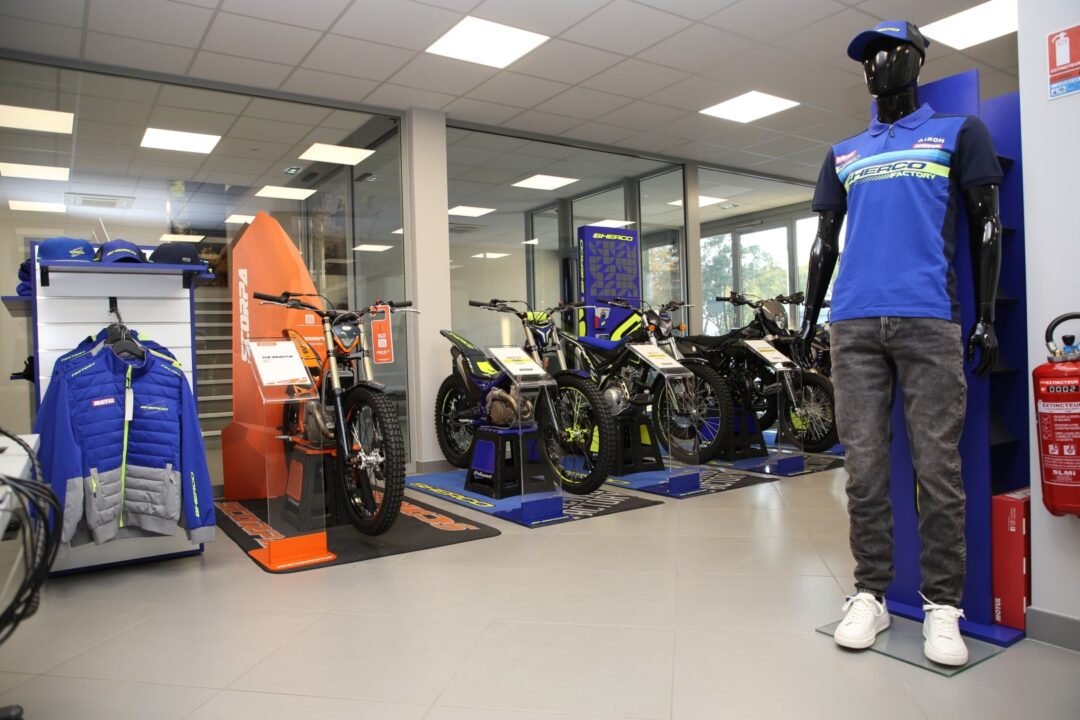
L’ingresso del polo produttivo vede un area nella quale sono esposti alcuni modelli oltre a capi d’abbigliamento, special parts ed altri prodotti marchiati Scorpa e Sherco.
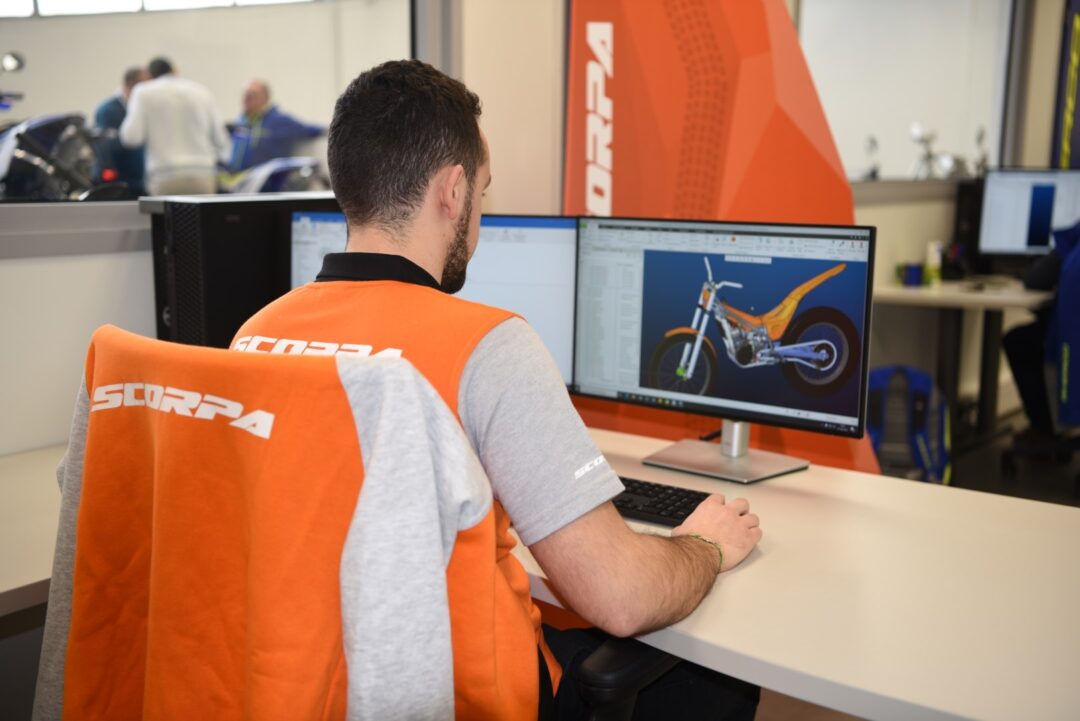
Al piano superiore, invece, vi sono gli uffici amministrativi ed il reparto progettazione e ricerca – sviluppo che è diviso in settori.
In questi ultimi, infatti, ogni persona lavora ad un progetto specifico confrontandosi con i colleghi.
L’area più ampia è quella produttiva che vede:
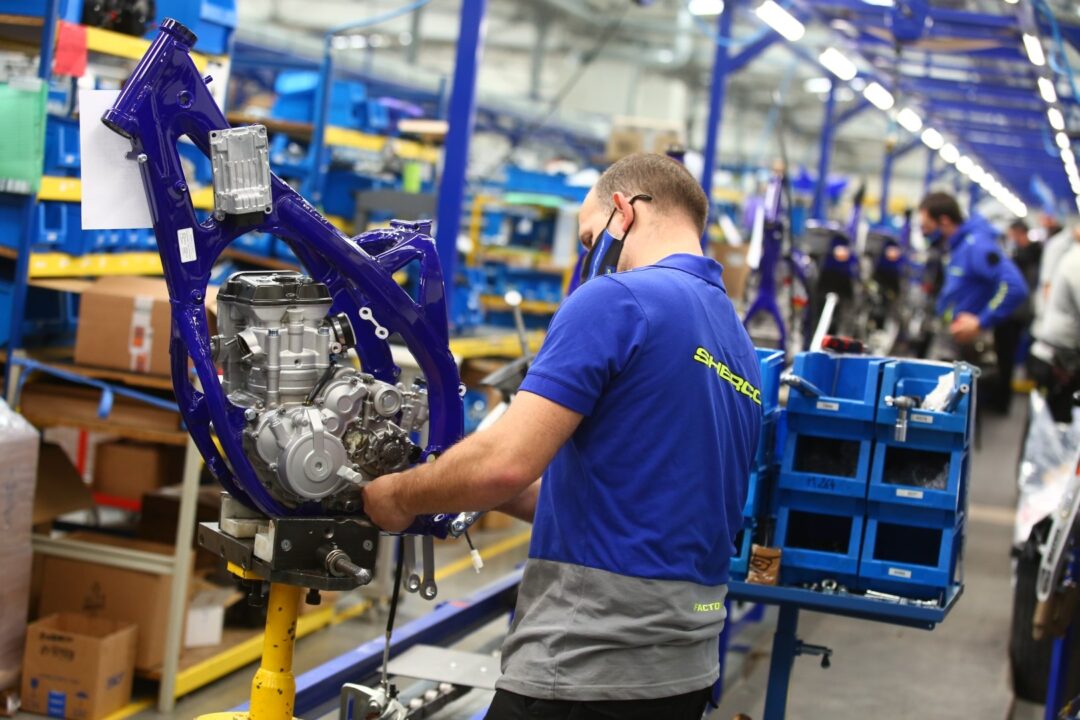
4 linee montaggio motori
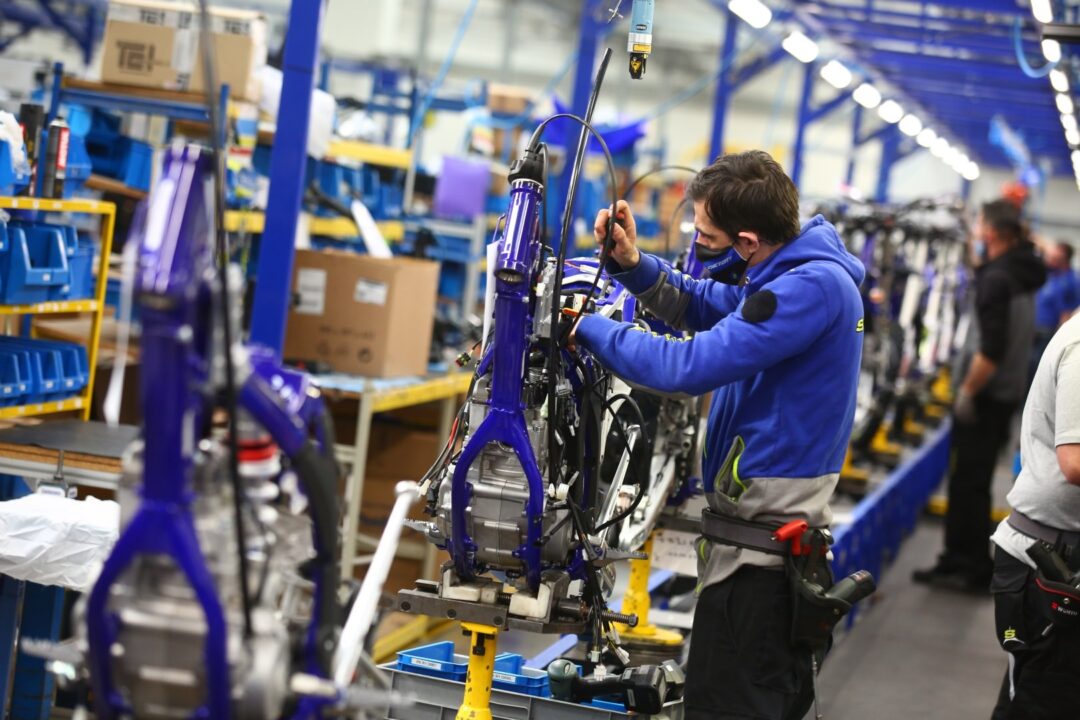
1 linea enduro
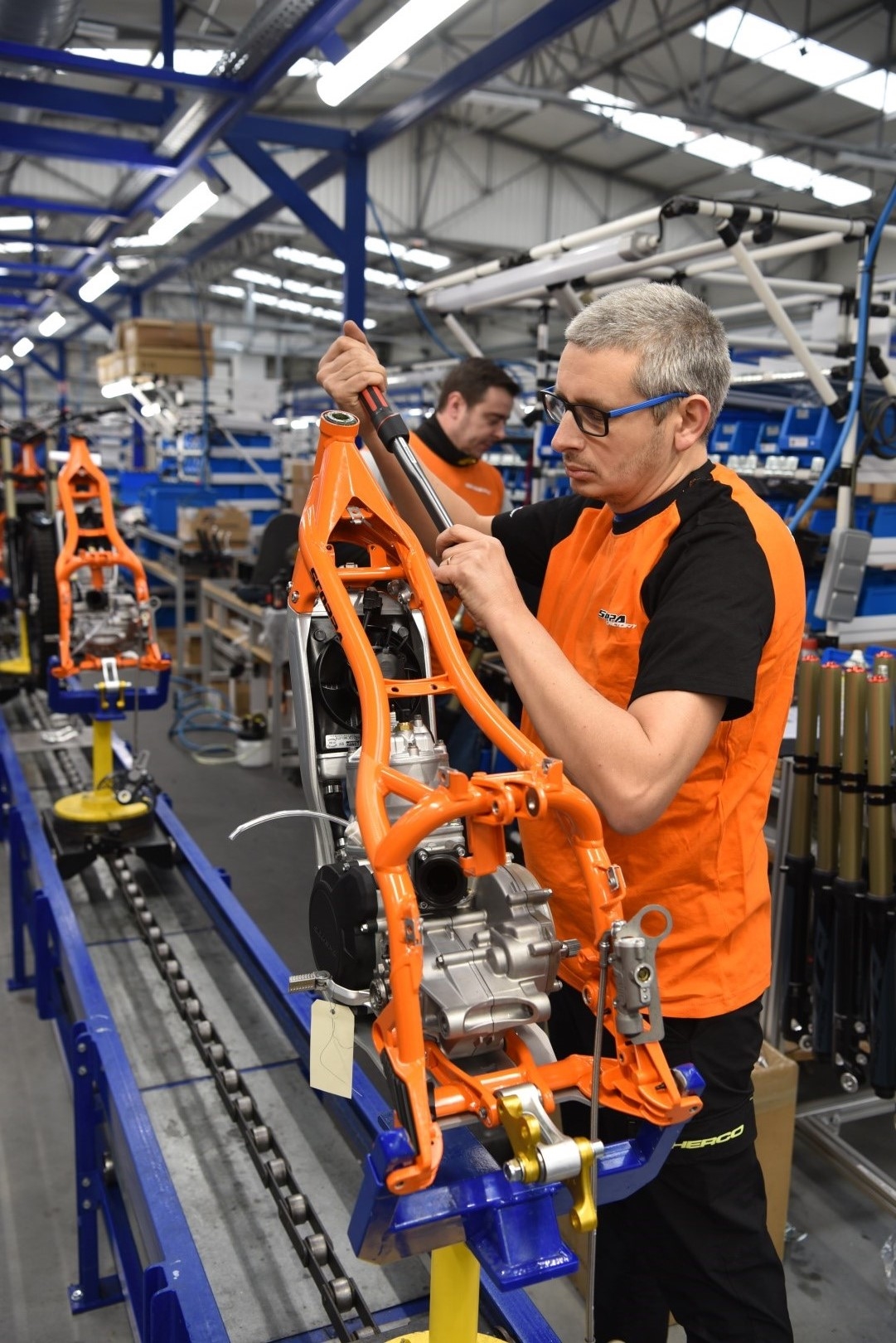
1 linea trial e 50 cc
I propulsori vedono 8 postazioni di montaggio motore dove ogni operatore assembla una parte per poi passarlo a quella successiva.
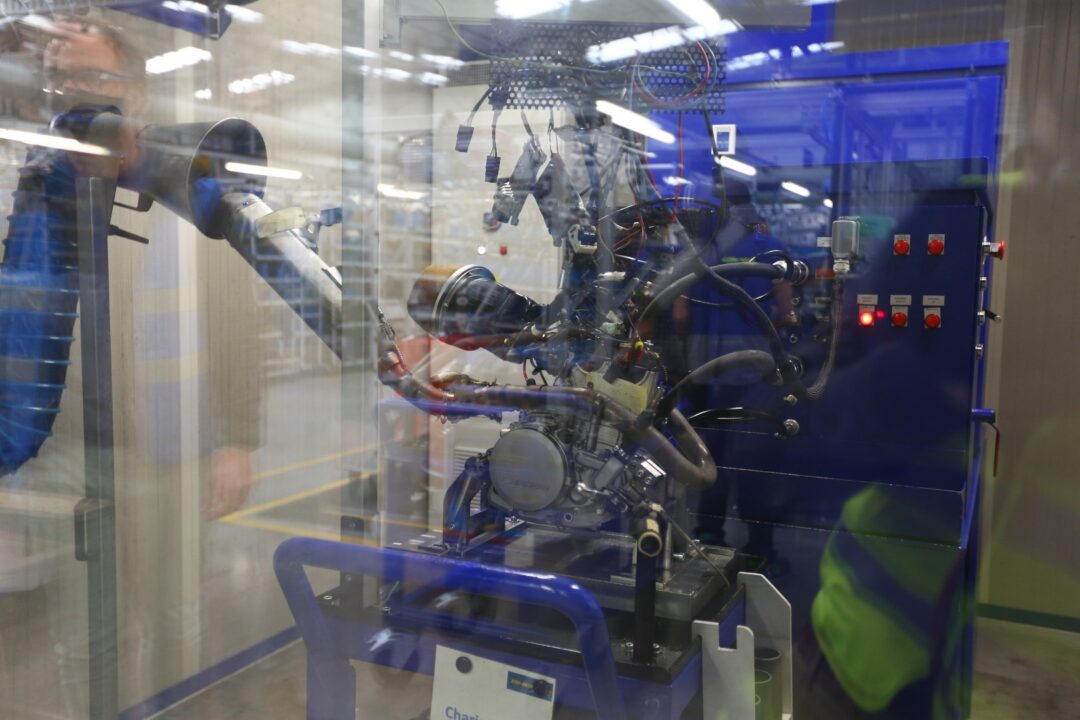
Terminato l’assemblaggio il propulsore viene testato per 15 minuti.
Nelle prove finali il motore, dopo essere stato montato su banchi prova e collegato ad un sistema di raffreddamento e monitoraggio elettronico, viene avviato.
In quest’ultima fase, dopo aver raggiunto la temperatura di esercizio, viene provato nei vari regimi di rotazione e su uno schermo viene verificato che le prestazioni siano in linea con quelle ideali (con una tolleranza del 2 per cento in più o meno).
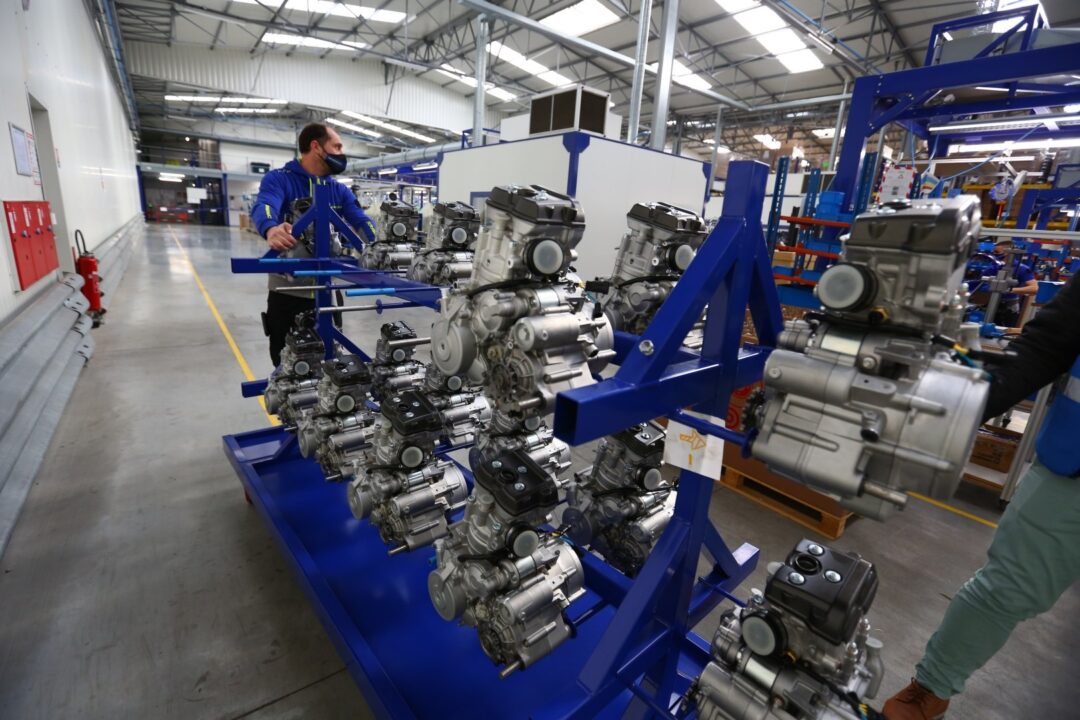
Sono 12 le stazioni di montaggio della moto completa ed ogni giorno possono essere prodotti 40 mezzi per un totale di 80 sulle due linee.
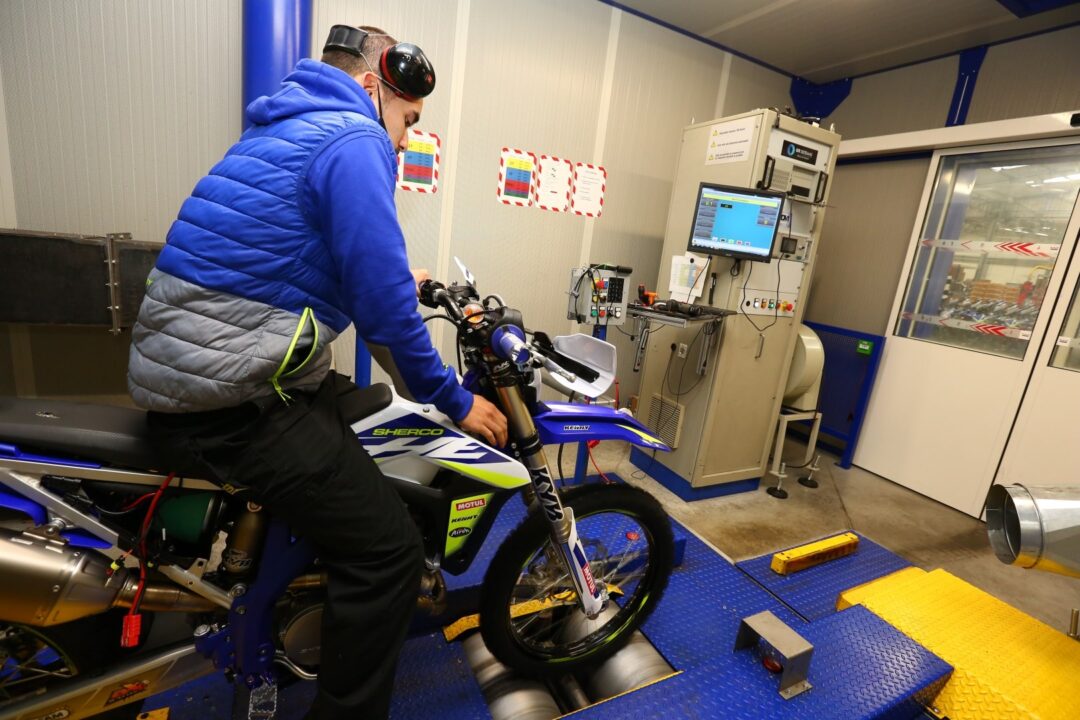
Finito il montaggio viene provata la moto completa per 10 minuti, tranne il motore.
Vengono testati l’impianto elettrico, freni e tutte le varie funzionalità.

Un impianto moderno che vede la produzione interamente visibile.
Infatti il materiale in ingresso, dopo essere stato scaricato dai camion, è soggetto al controllo qualità e quantità.

Successivamente viene stoccato nel magazzino.
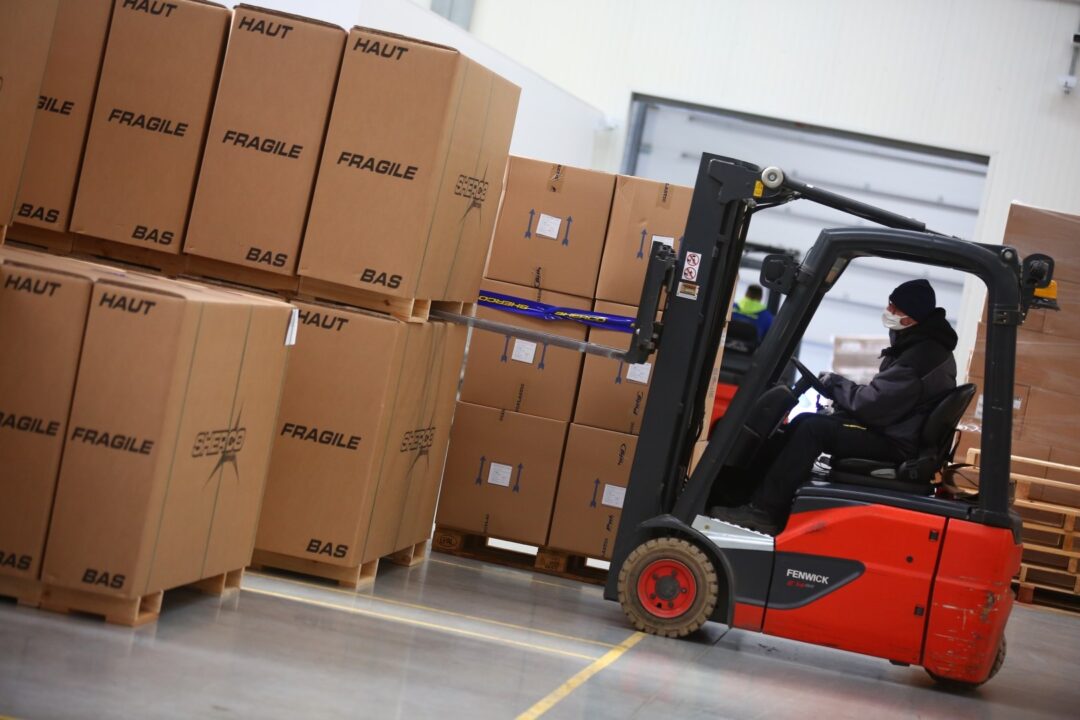
Inviato alla linea d’assemblaggio-montaggio e dopo i controlli finali la moto viene imballata ed è pronta per essere spedita.

Vi è poi un reparto dedicato all’invio dei ricambi dove il 90 % dei pezzi ordinati entro le ore 10 vengono spediti in giornata al richiedente.
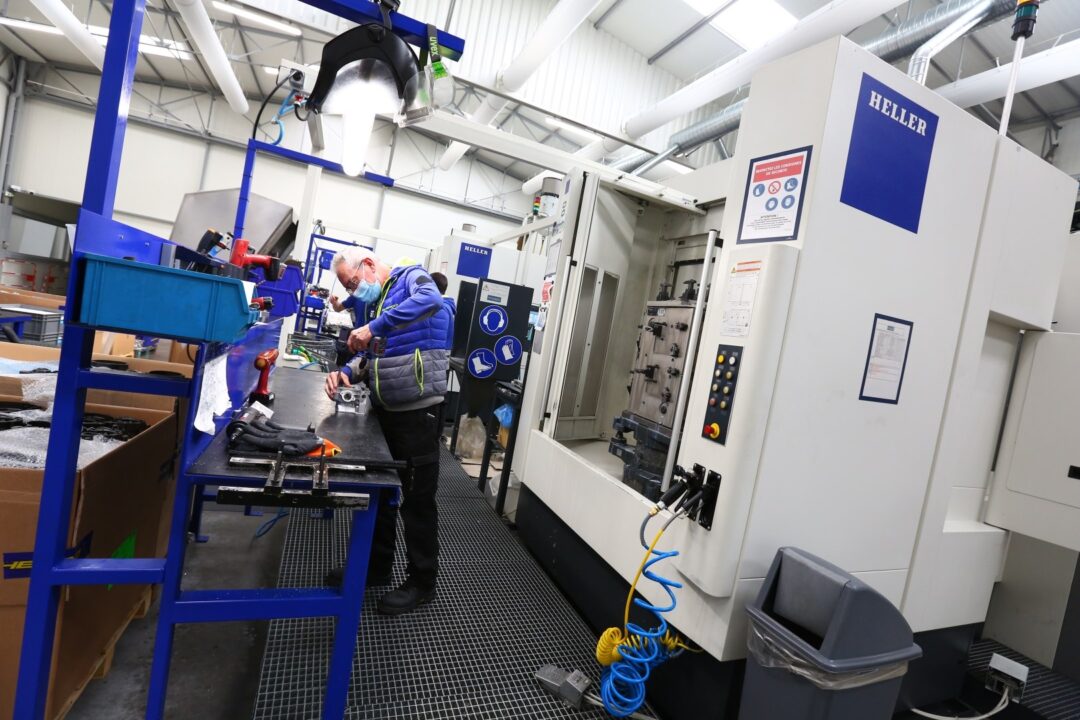
A poche centinaia di metri dallo stabilimento principale, da circa un anno, vi è la struttura che lavora i pezzi grezzi e vengono prodotti gli ingranaggi.
Qui lavorano 11 persone.
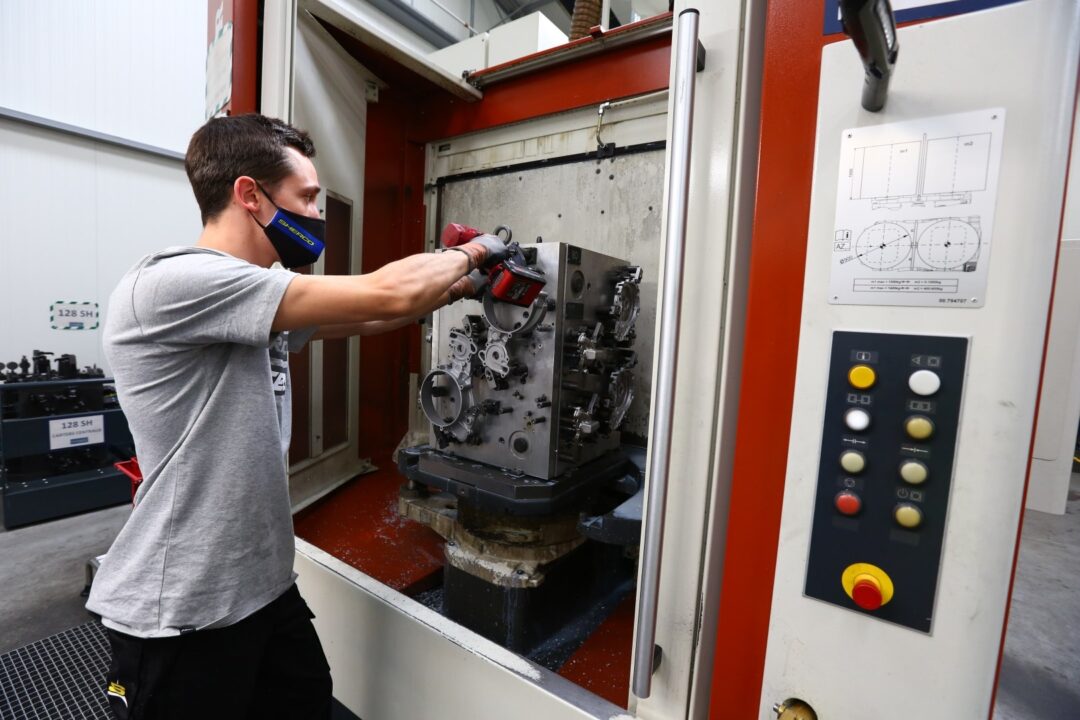
Ed è in questo distaccamento che vengono svolte le lavorazione dei pezzi grezzi da fonderia utili per il successivo montaggio.
Una scelta, quella di un capannone dedicato, dettata da questioni di spazio, infatti, qui in un’area separata vengono stoccate le moto per la spedizione.
Nel nuovo capannone lavorano robot che lavorano per 14 ore al giorno.
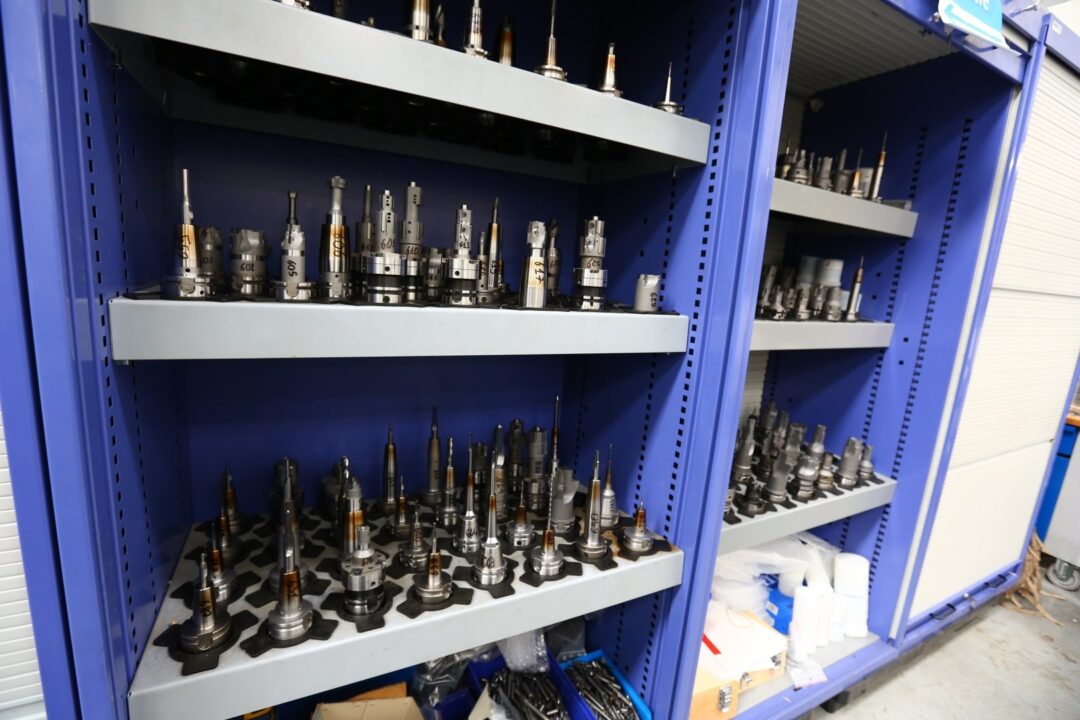
Diversi macchinari svolgono le varie fasi della produzione:
Tornio per tornitura dura ingranaggi al posto della rettifica
Dentatura interna
Dentatura esterna
Dentatura a creatore
I macchinari impiegano morsetti di vario tipo in base al tipo di ingranaggio da produrre.
Vi è una postazione di tornitura con due mandrini per fare un lato e l’altro
Una volta terminate le lavorazioni il pezzo viene lavato per eliminare impurità.
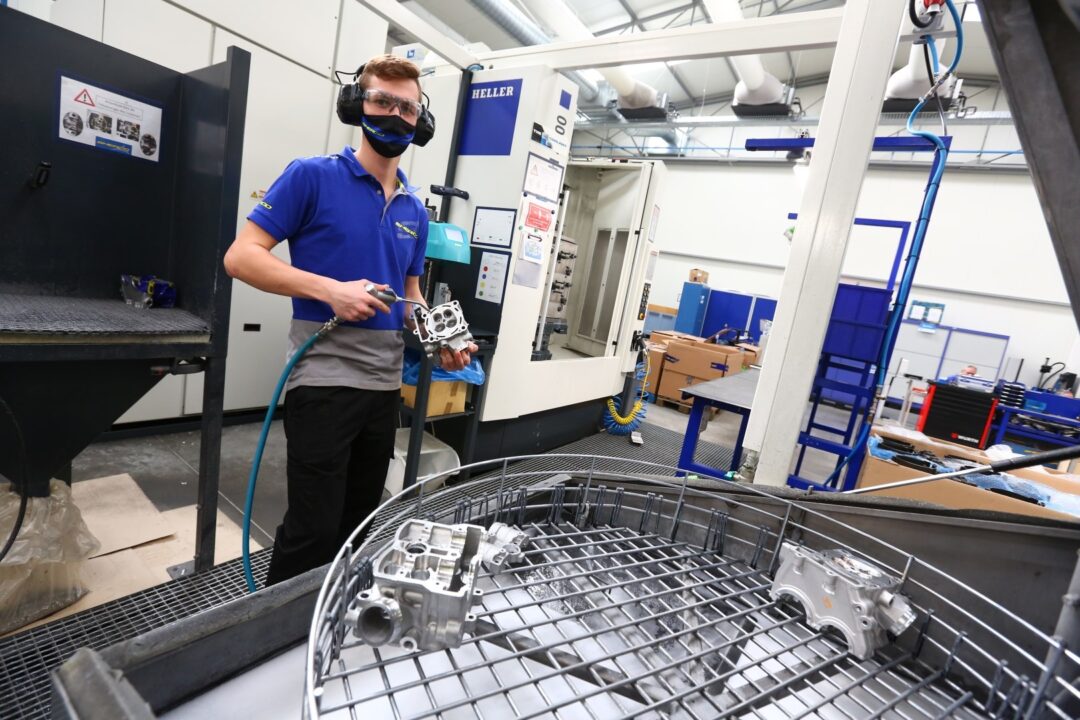
Successivamente viene inserito in un Forno (capacità 500 kg compreso l’attrezzo) per la cementazione con raffreddamento utilizzando l’azoto e cementificazione a bassa pressione.
I pezzi che compongono il cambio completo (circa 2,5 kg) vengono lasciati in forno per tre ore.
La fase conclusiva è quella della tempera per ridare resistenza.
Le operazioni per eliminare gli scarti di lavorazione, operazione che dura circa 5 minuti, richiede però un lungo lavoro di posizionamento dei pezzi e viene svolto da un’azienda esterna.
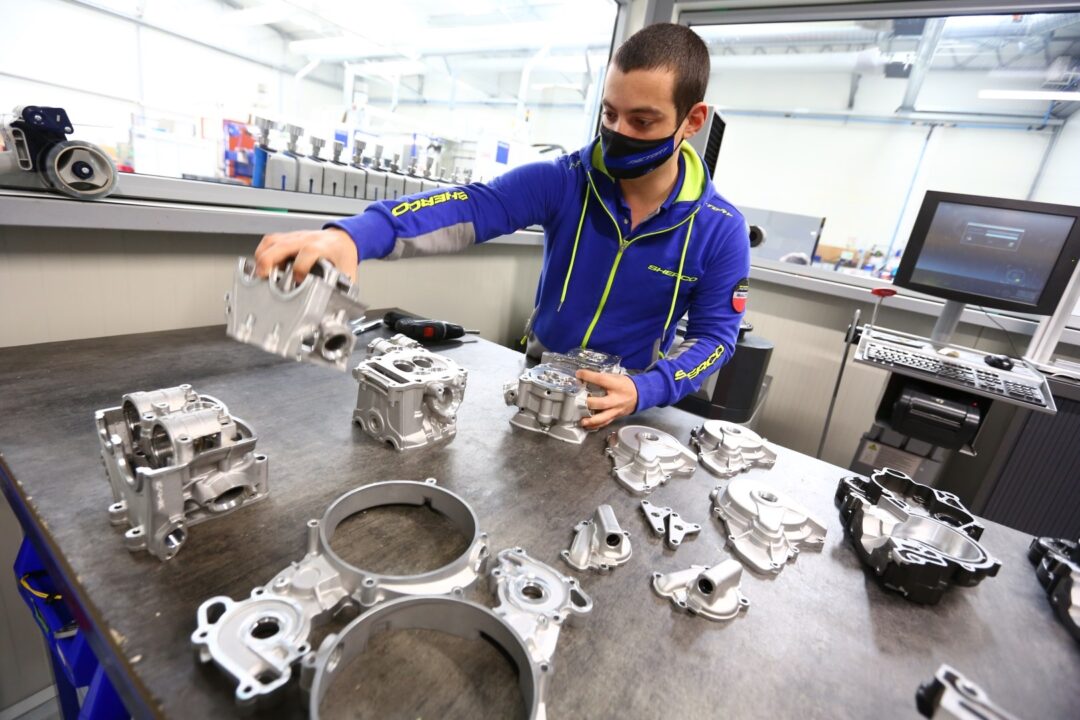
Non manca il controllo qualità che avviene per il primo pezzo prodotto, durante la produzione, per l’ultimo della giornata ed ogni volta che avviene un piazzamento di un pezzo.
Infine qui viene montato il cambio e poi su una dima viene controllato che sia montato correttamente
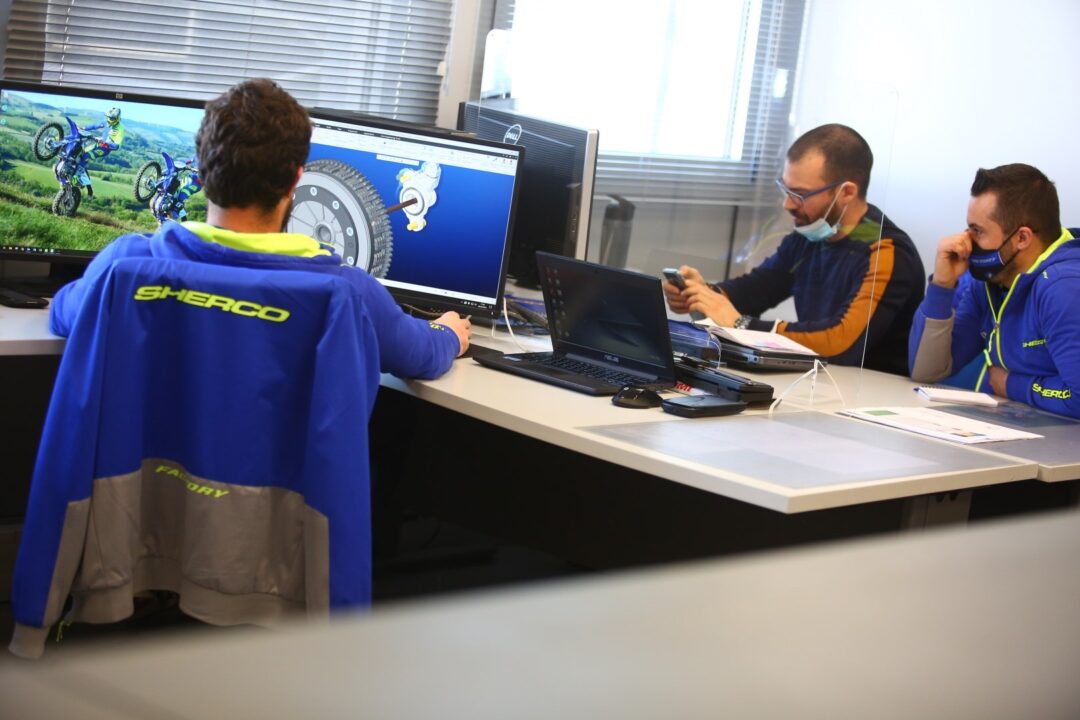
Non manca, infine, un area dedicata alla prototipazione.
Si conclude così la visita allo stabilimento dove prendono forma le Scorpa e Sherco.
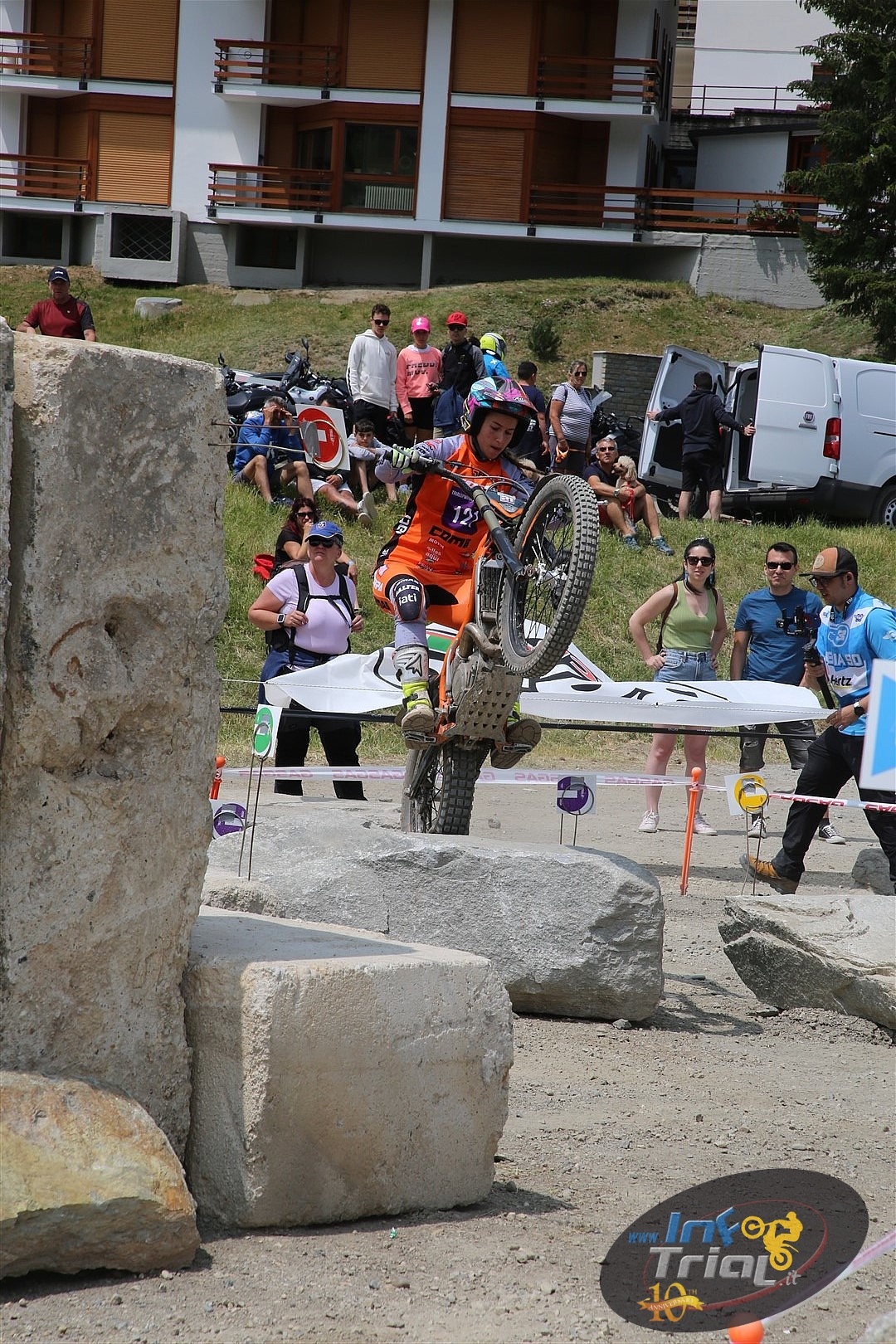
Mezzi che nel 2024 saranno condotti da tre campioni del mondo ed una vicecampionessa; stiamo parlando di Adam Raga ed Emme Bristow con i colori Sherco e Billy Green e Berta Abellan alla guida delle Scorpa.
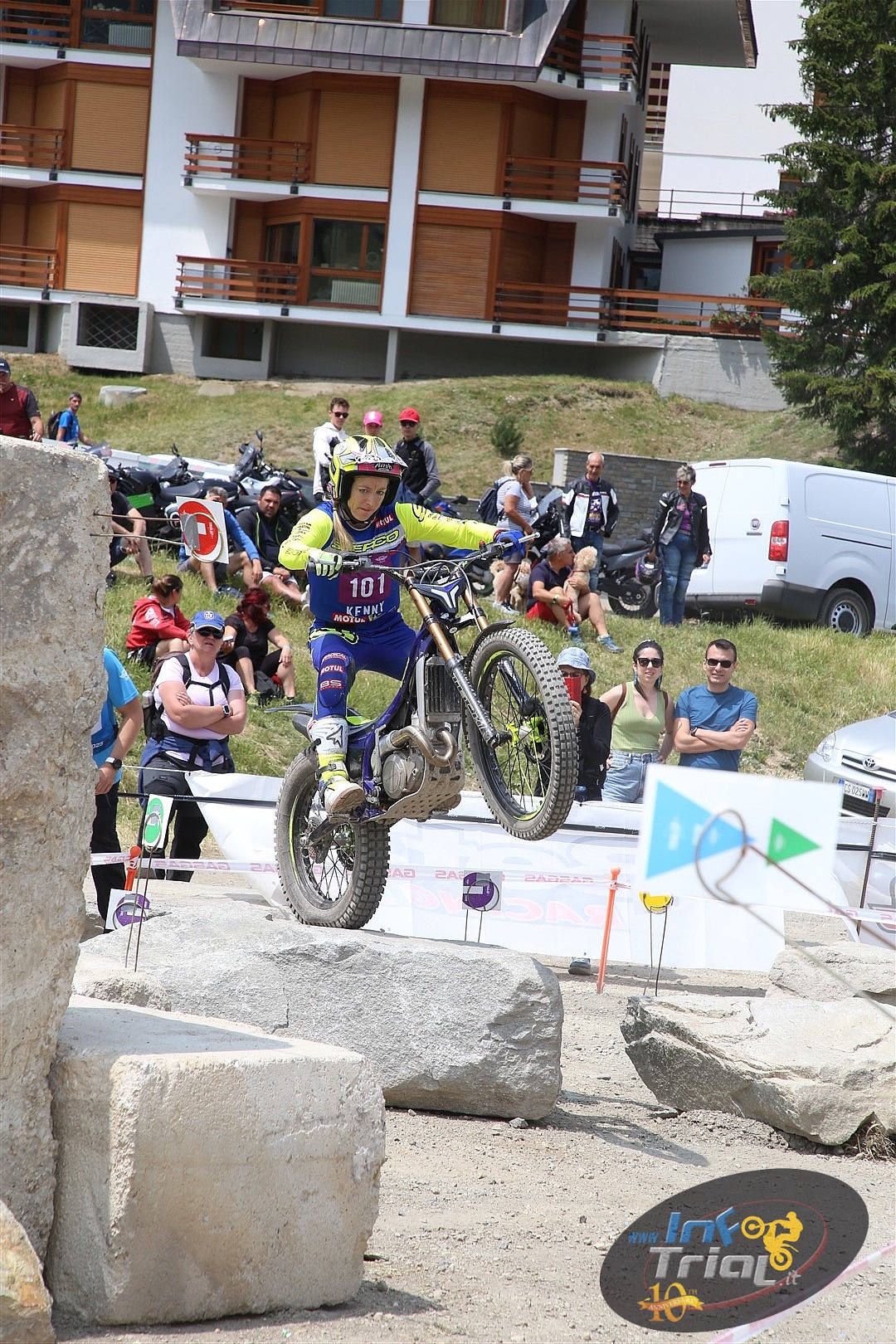
GALLERIA IMMAGINI
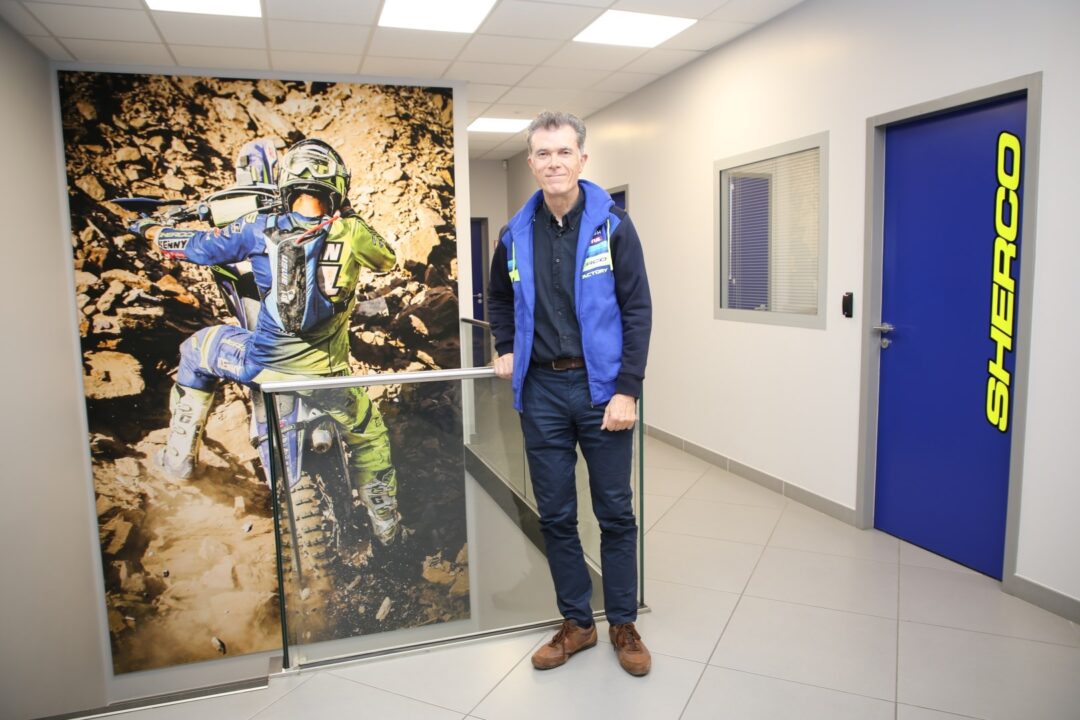
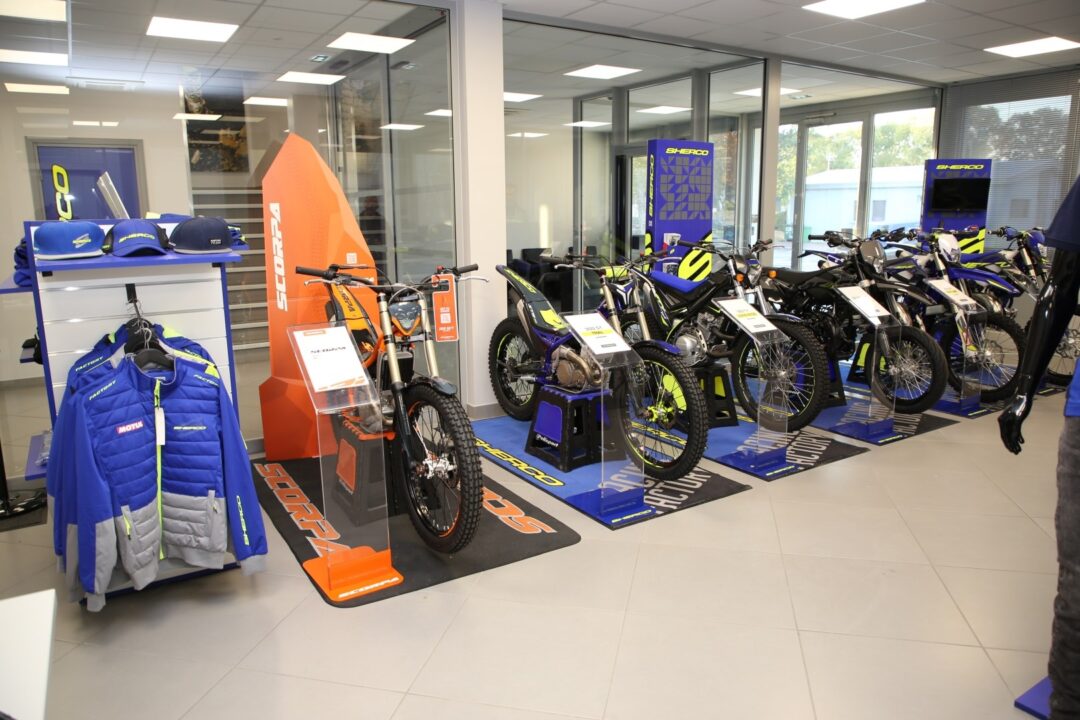
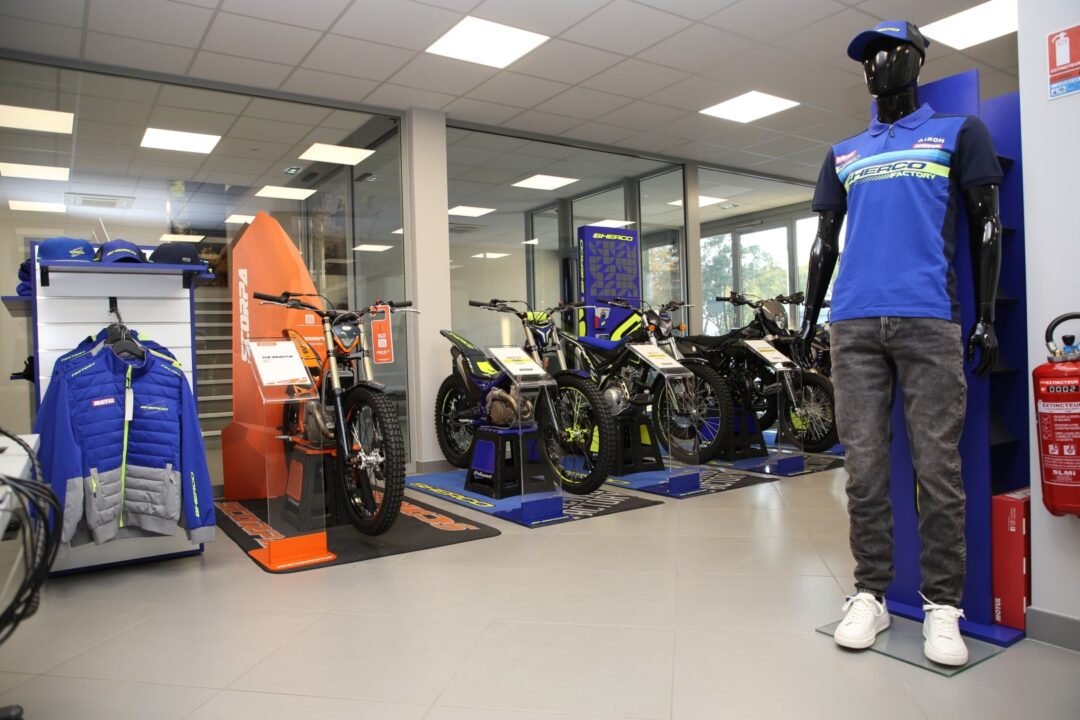
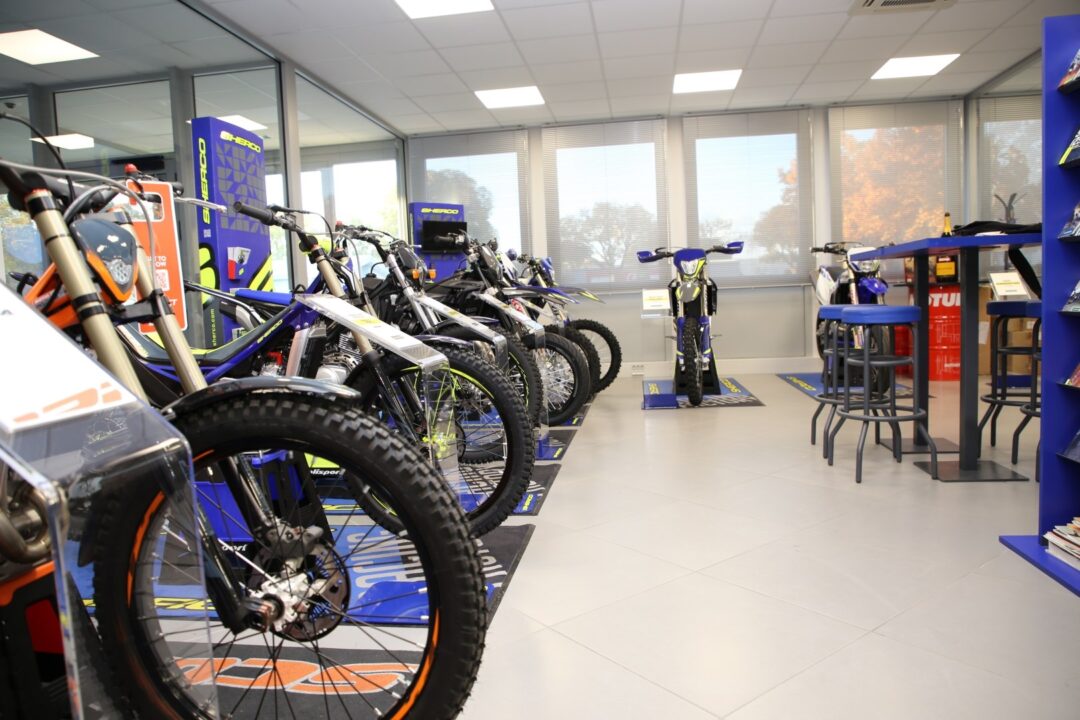
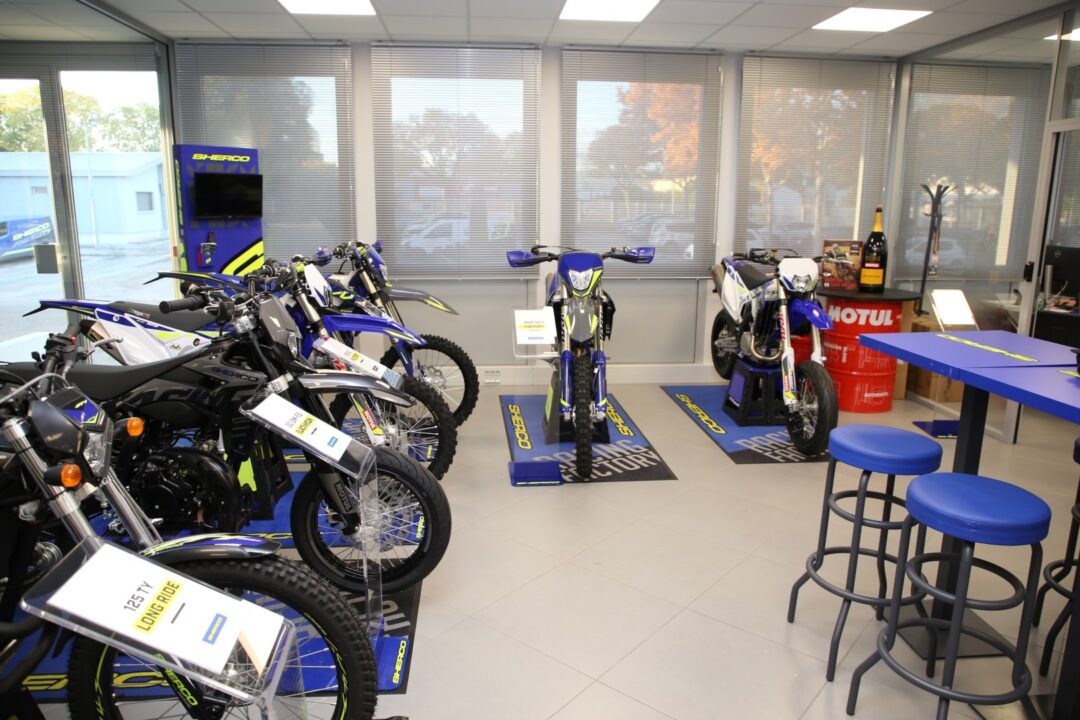
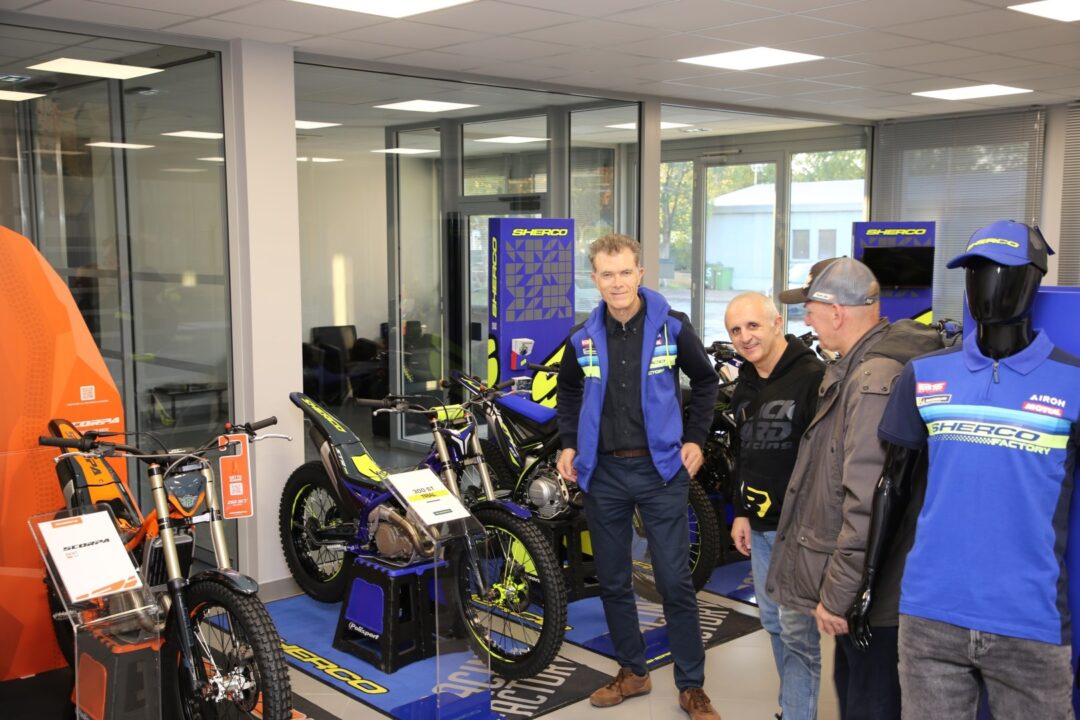

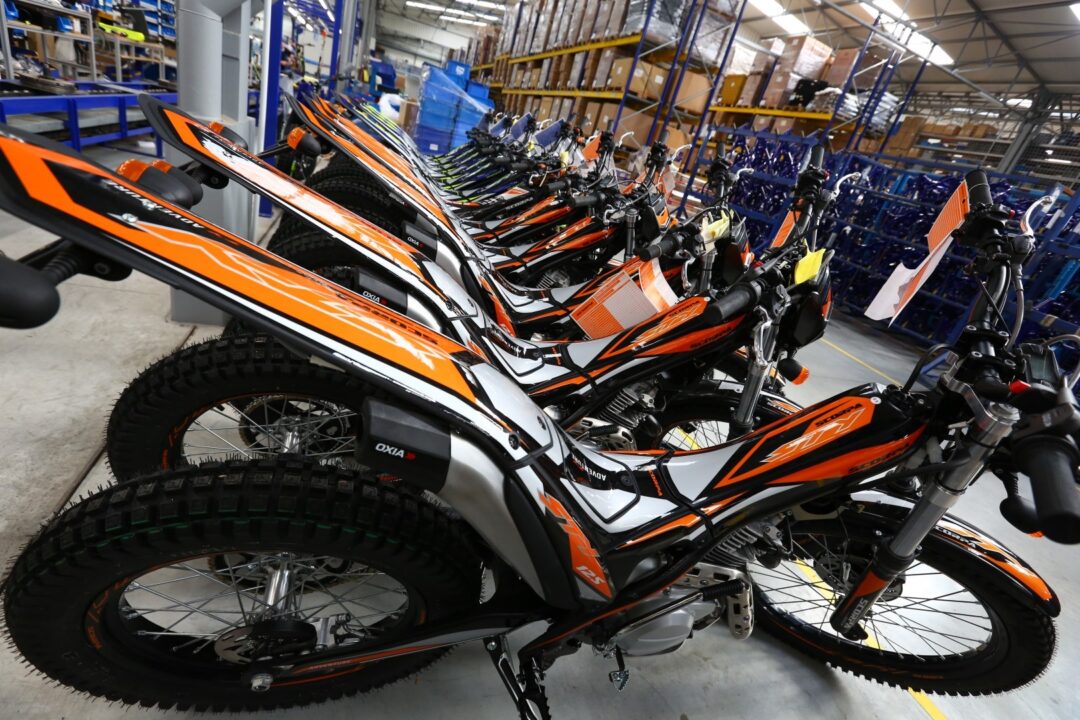
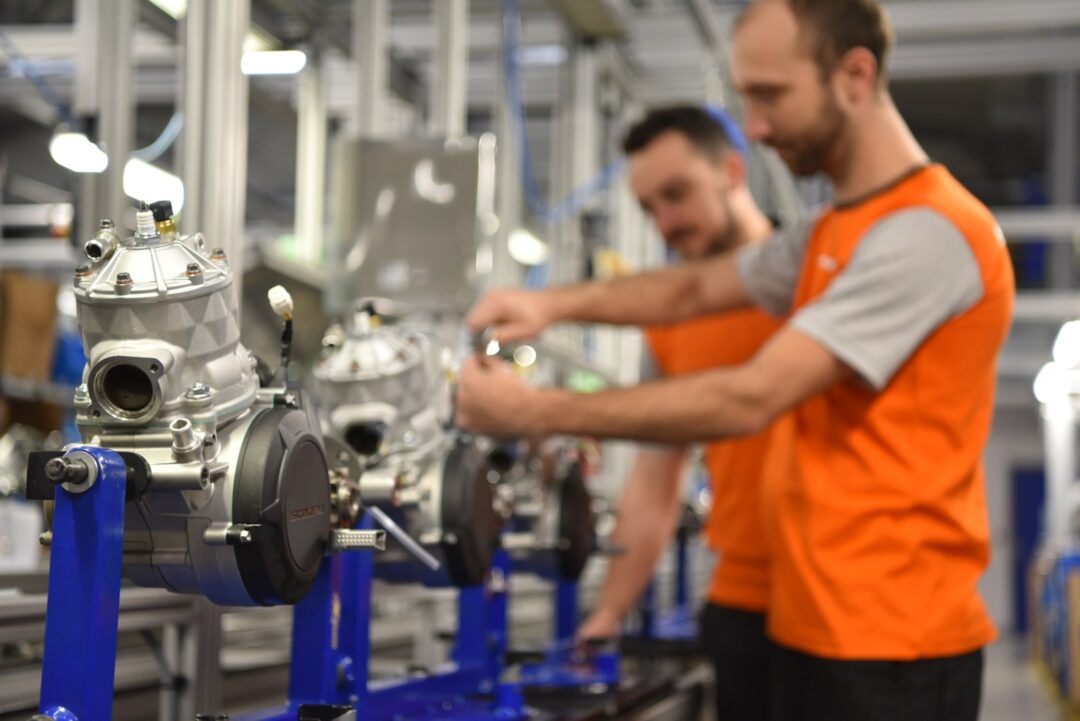
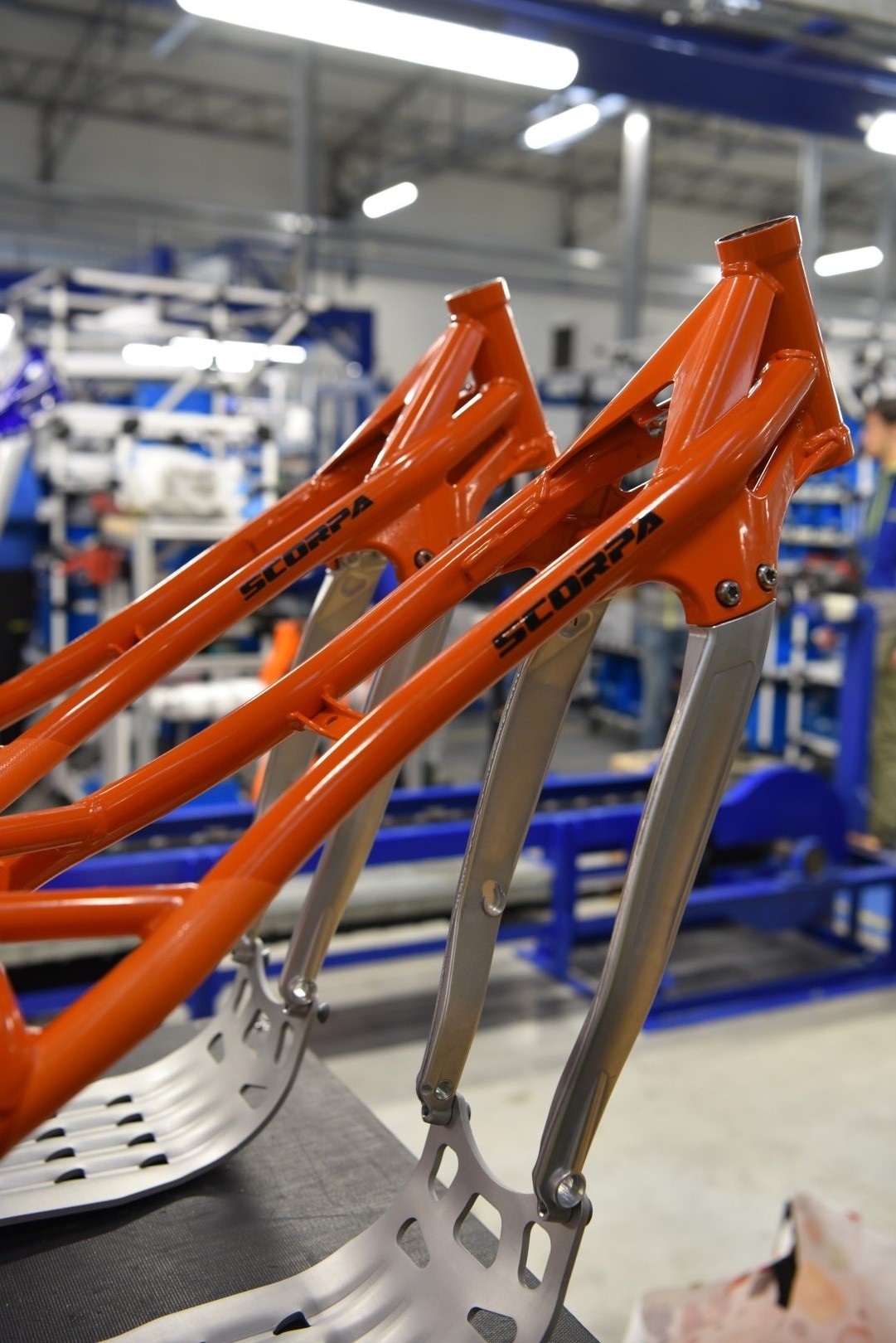
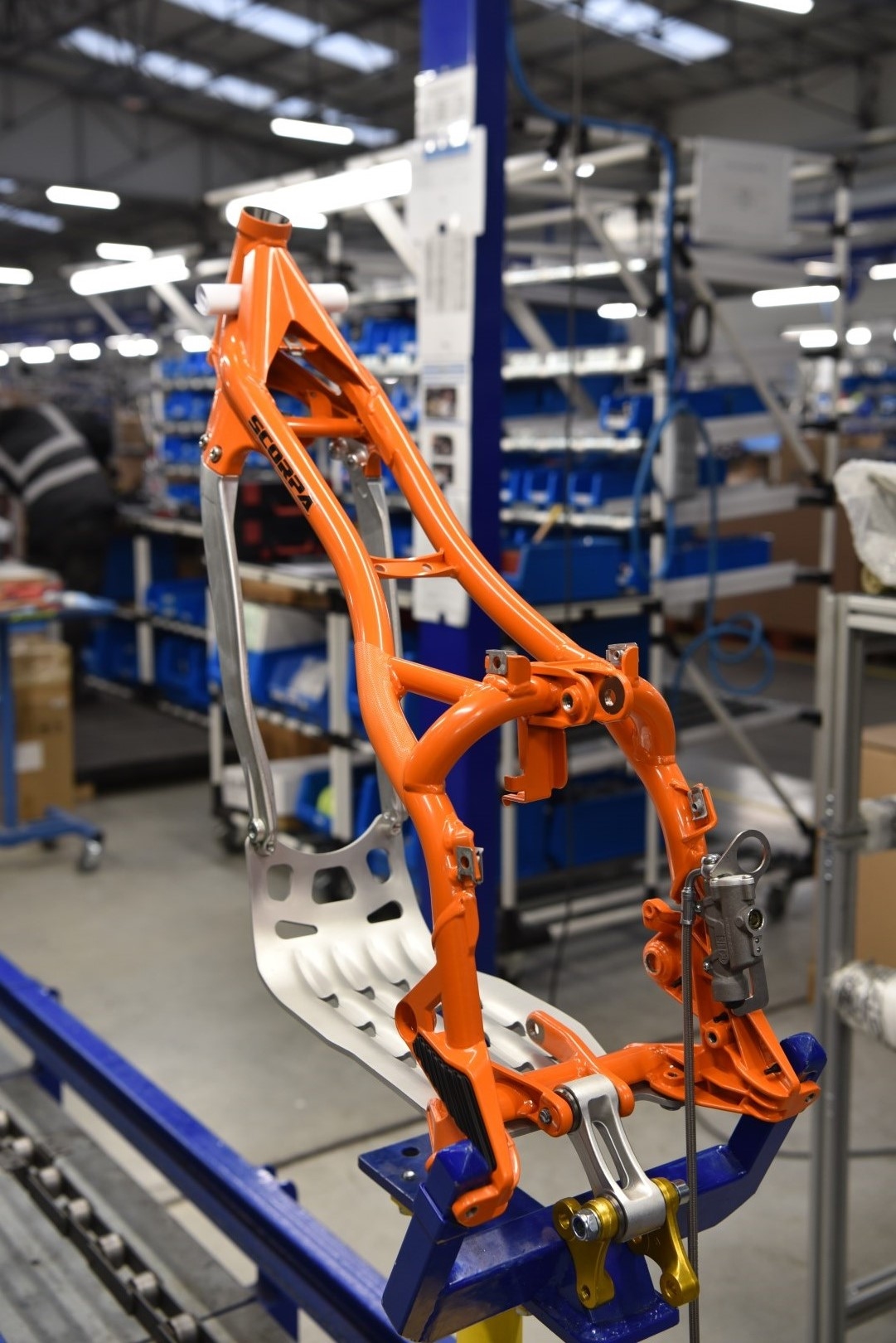
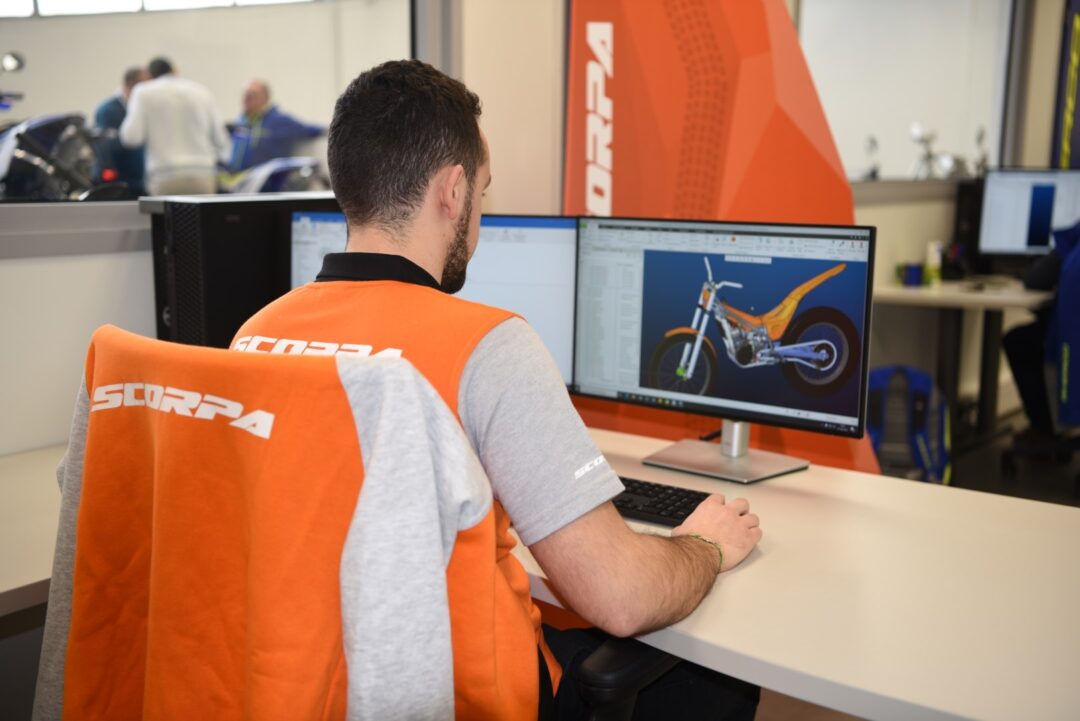
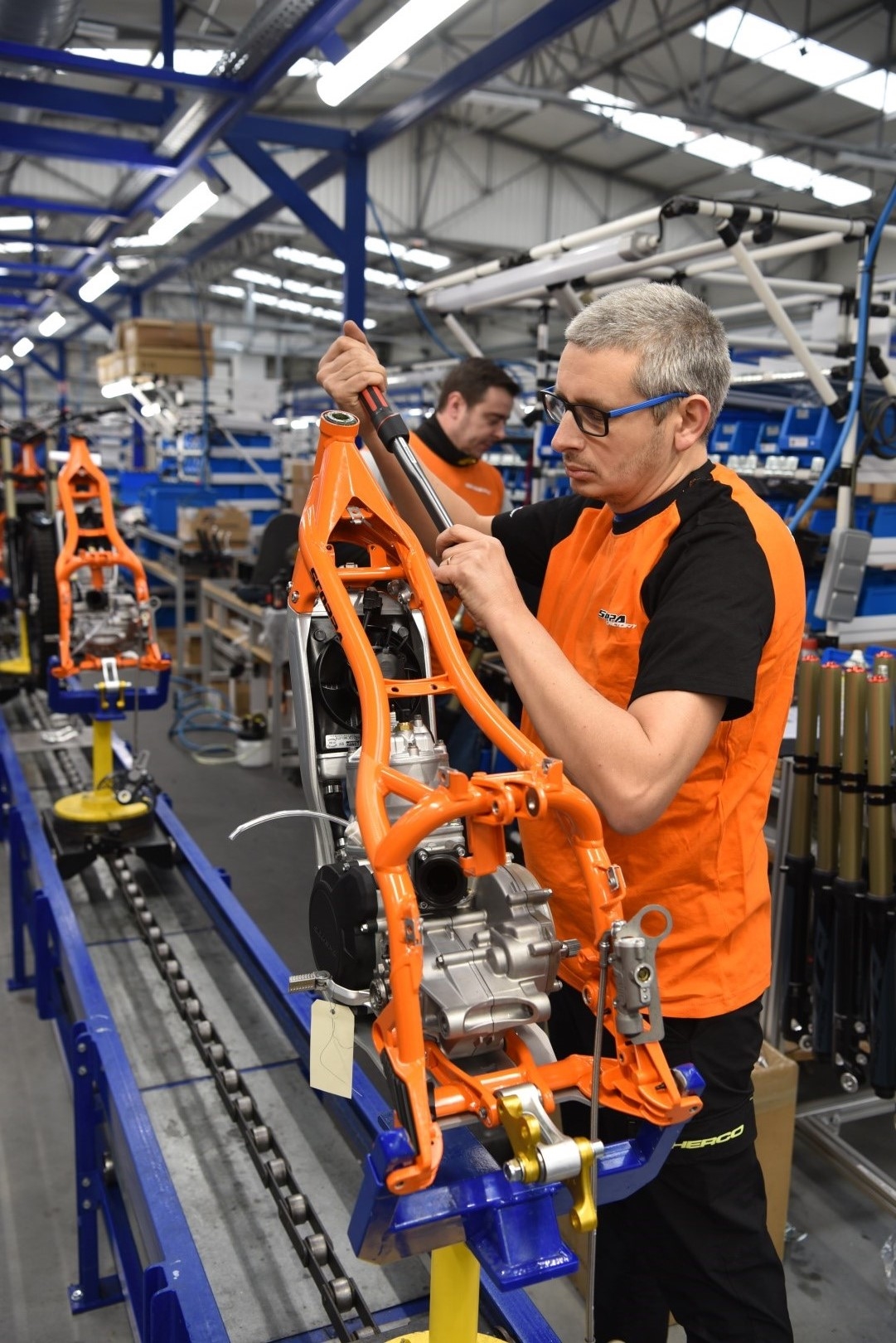
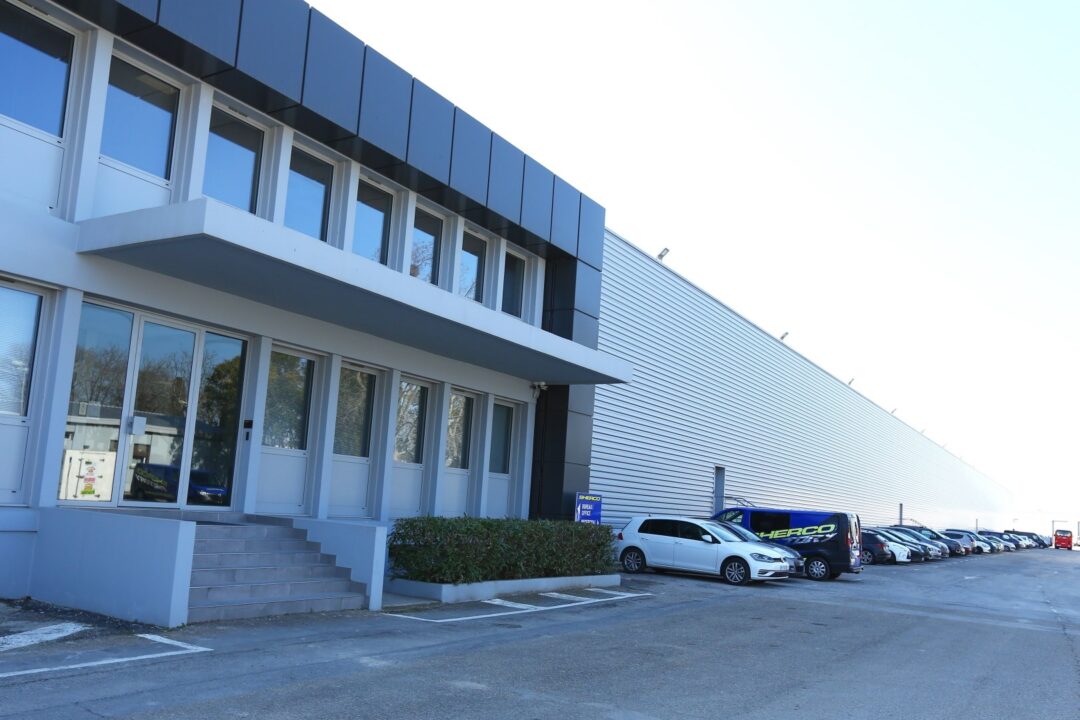
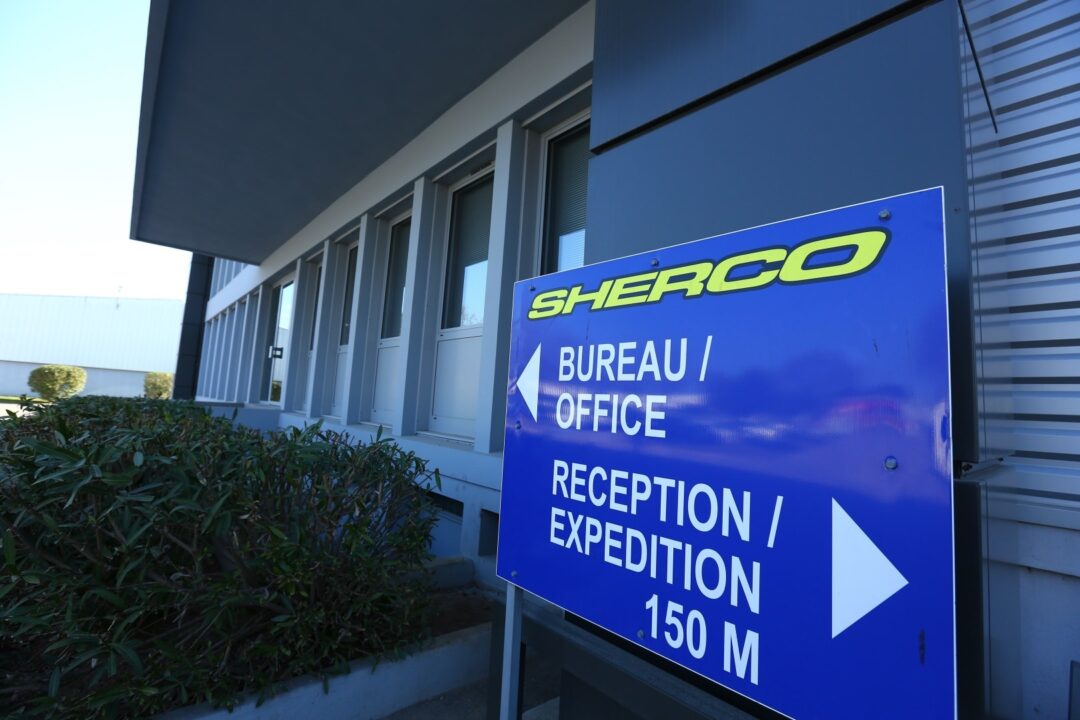
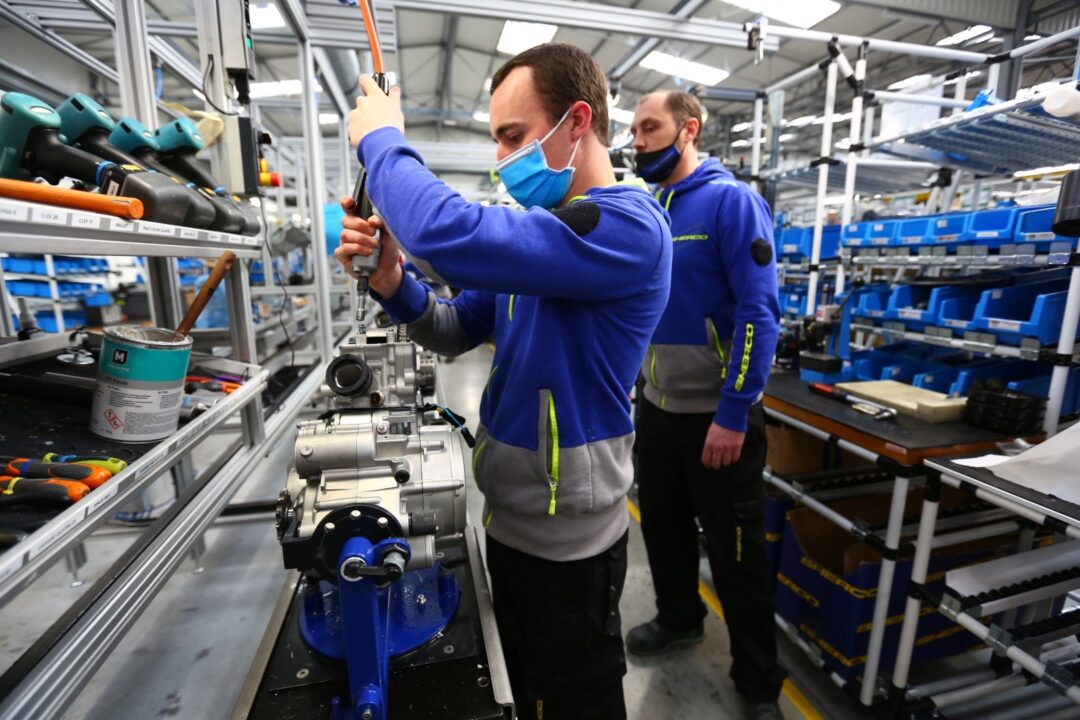
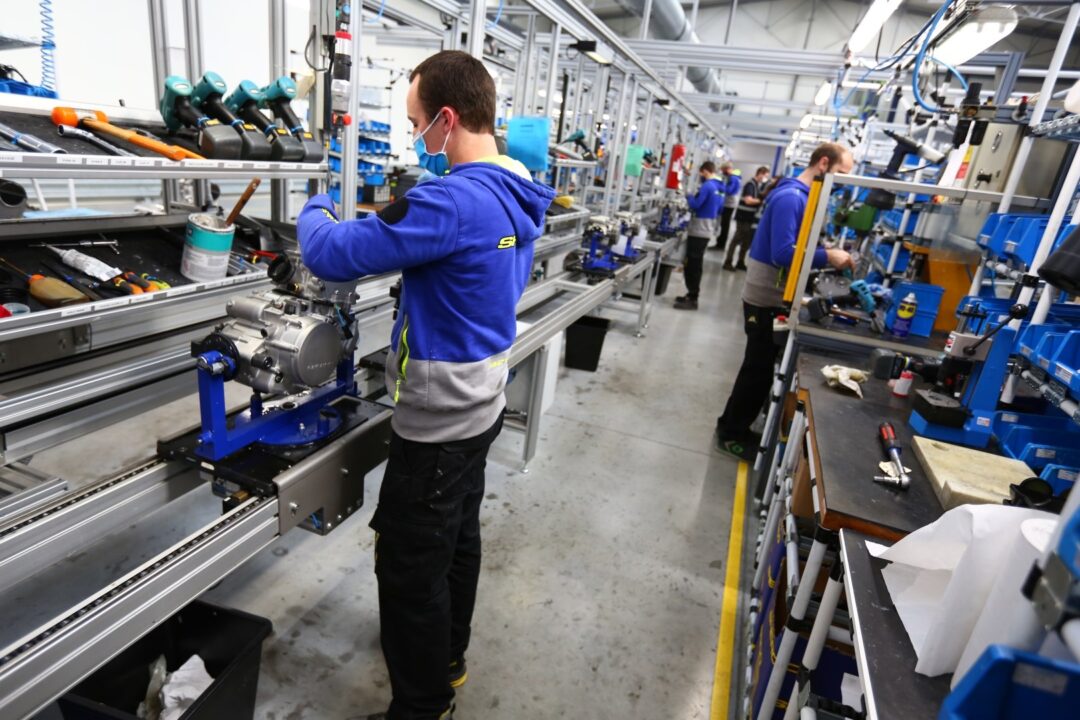
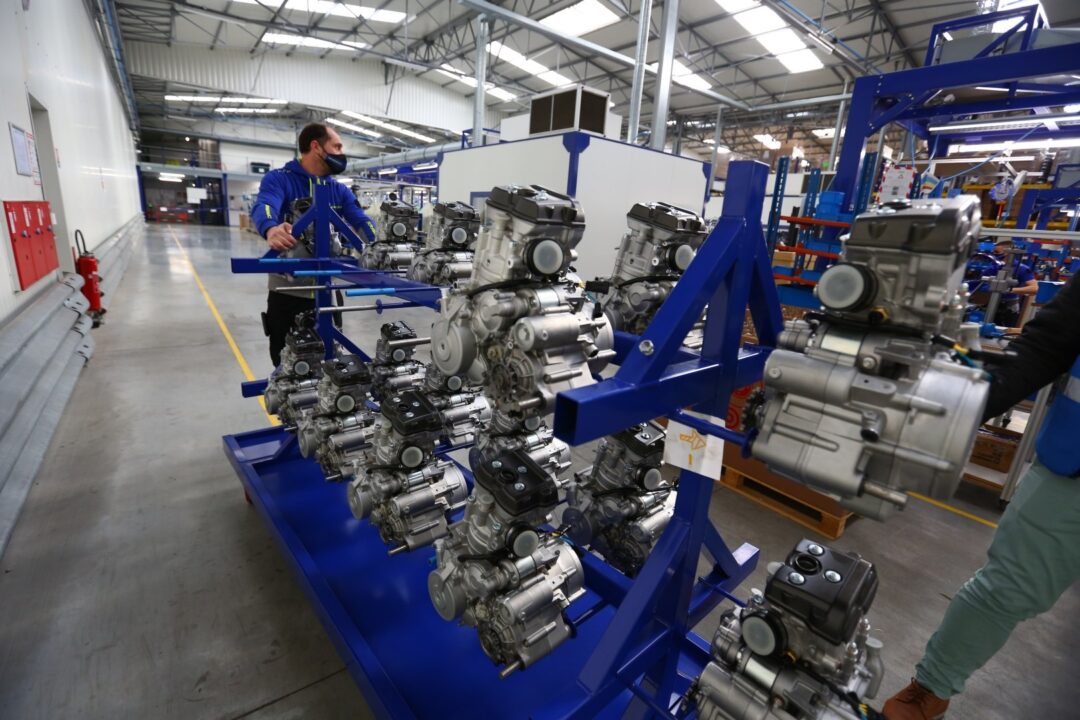
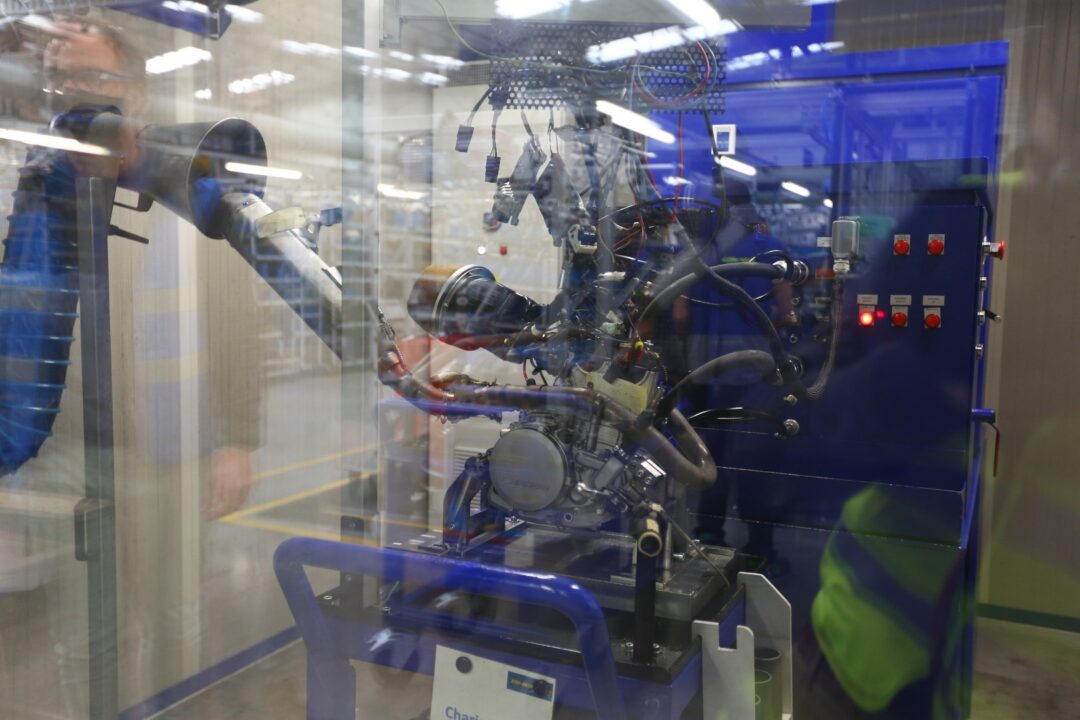
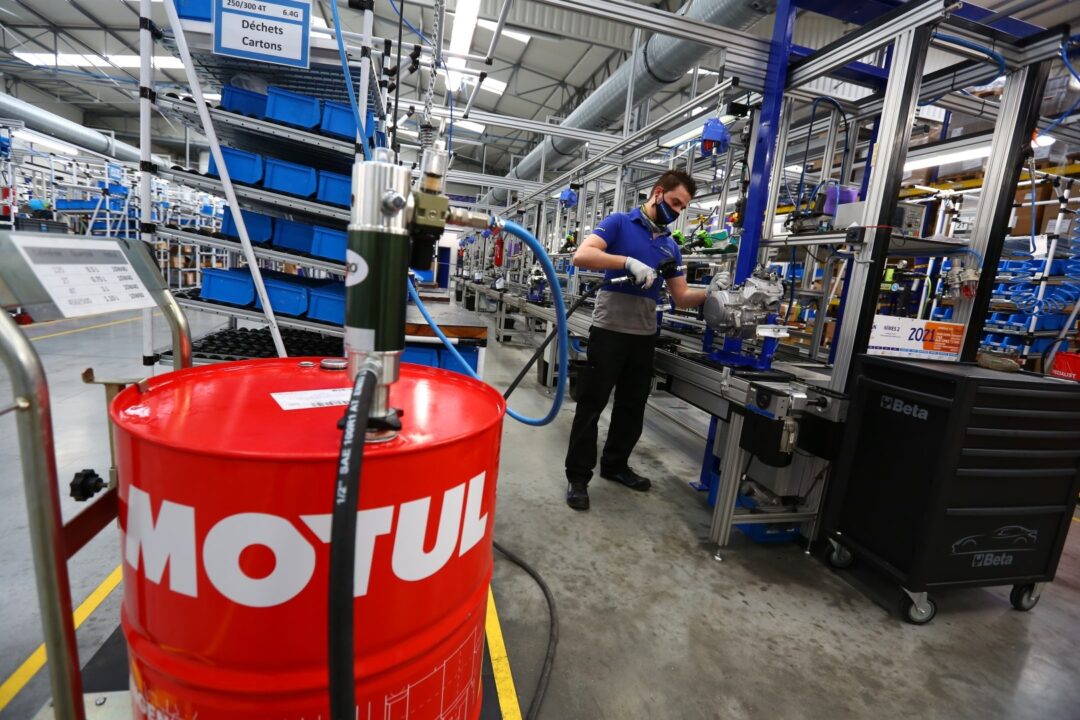
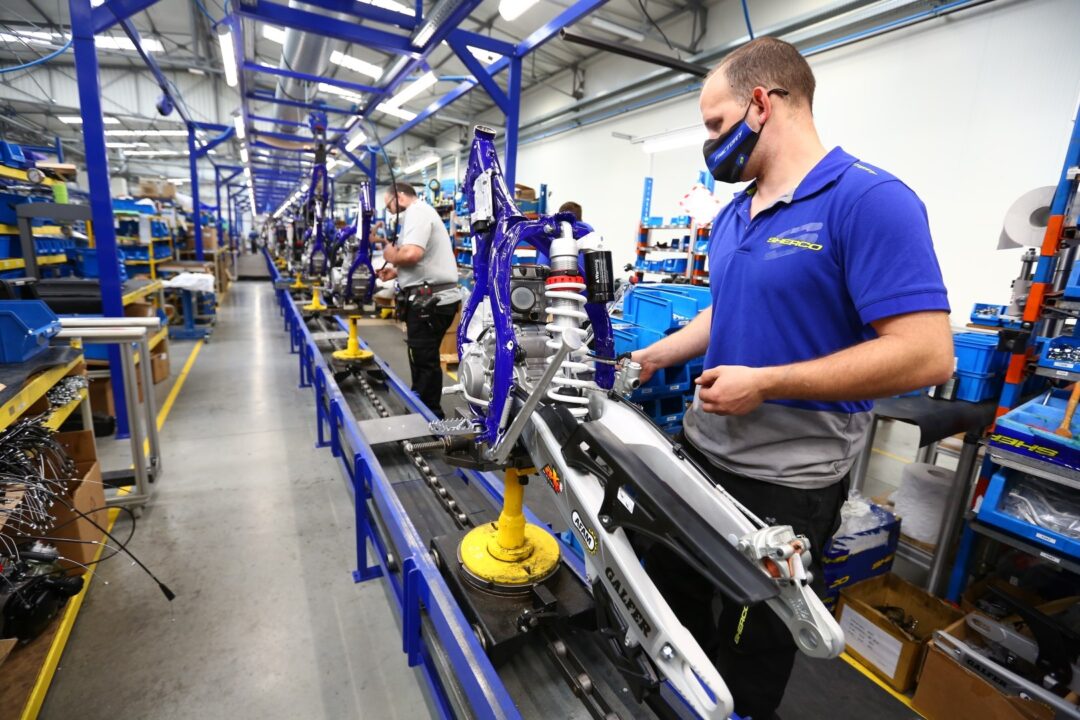
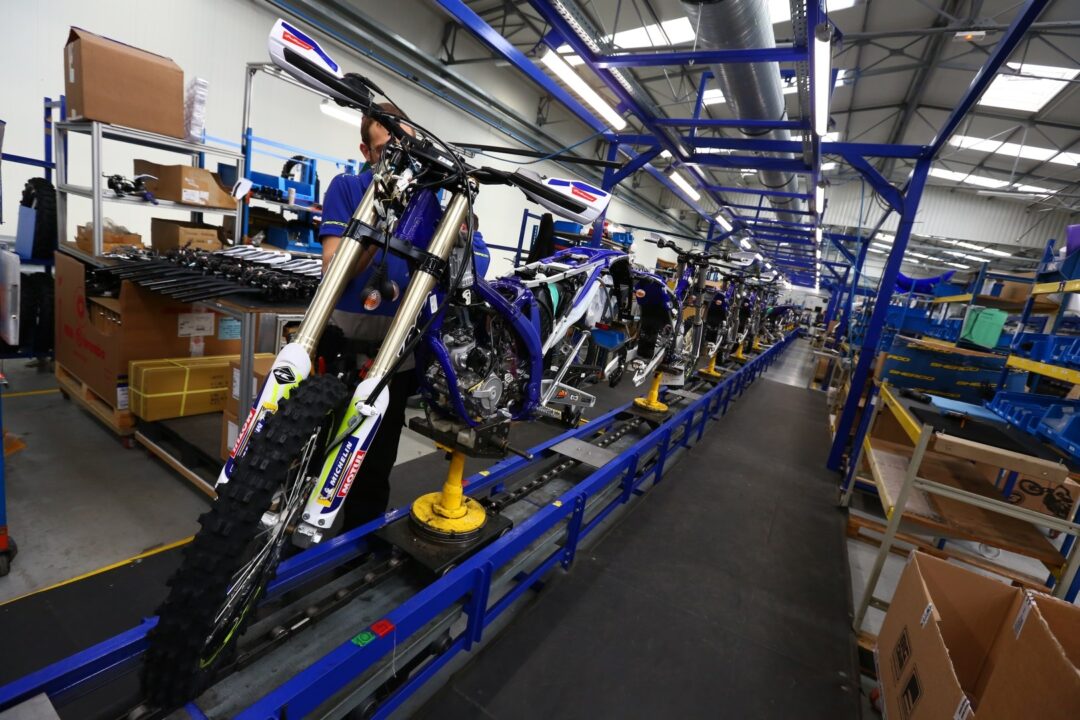
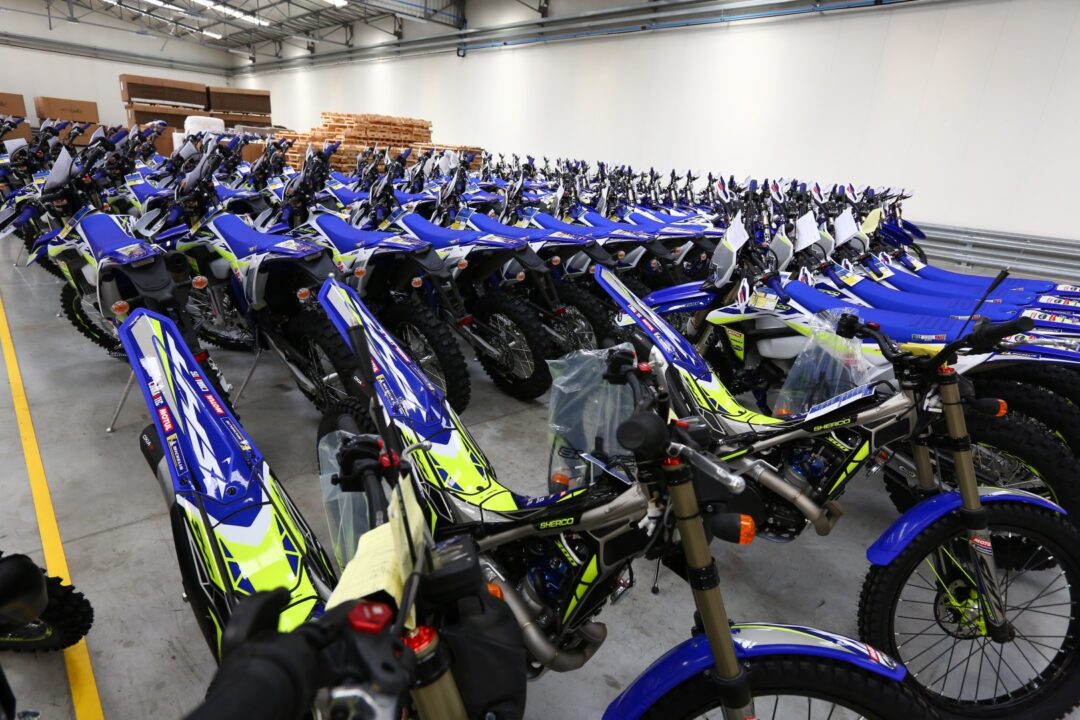
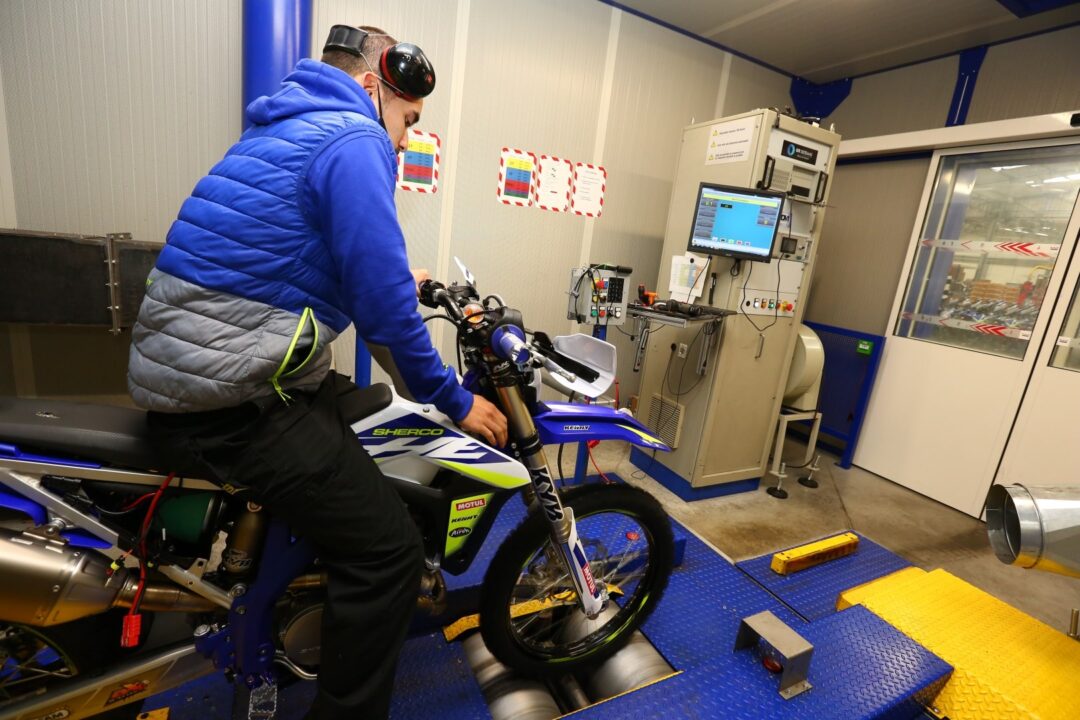
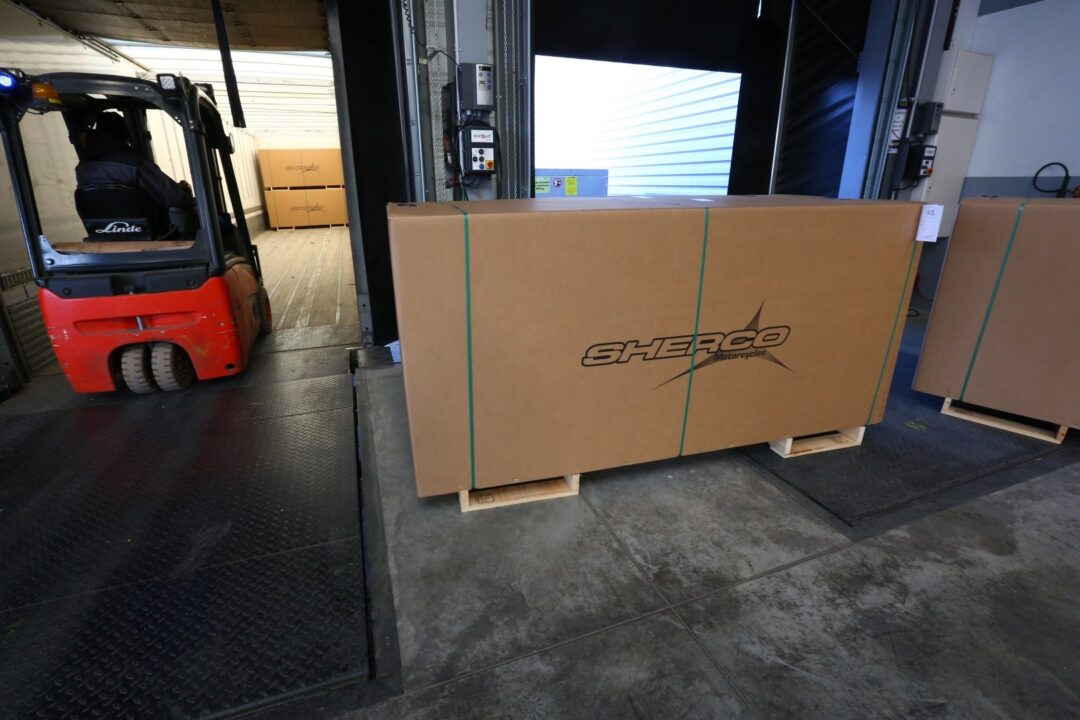
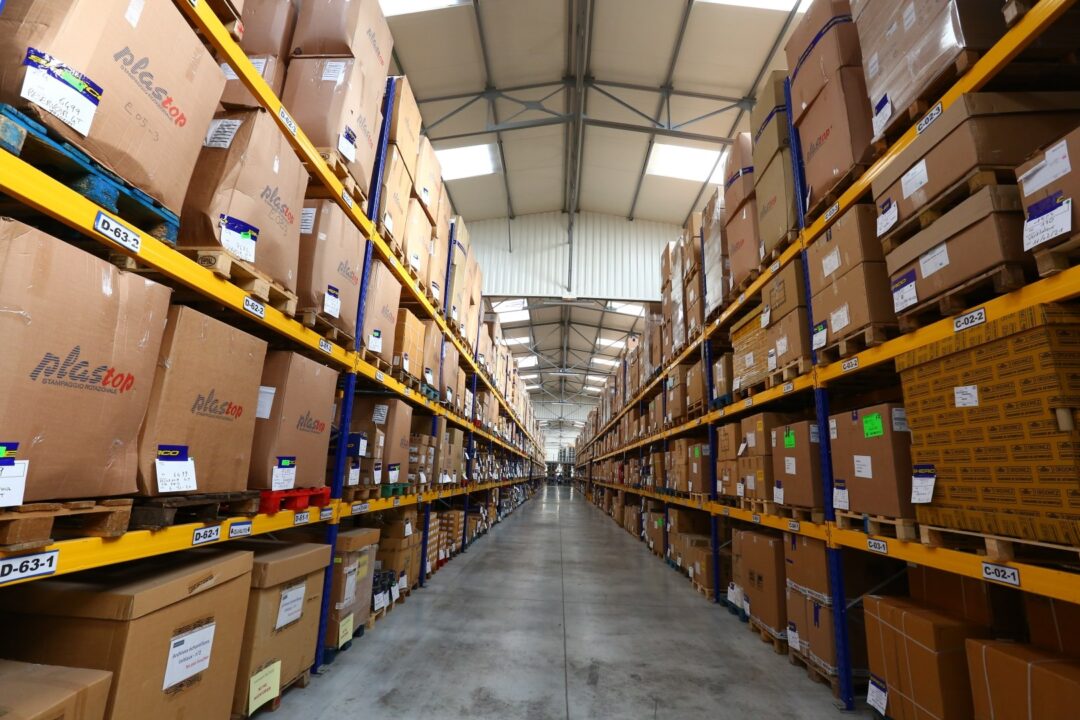

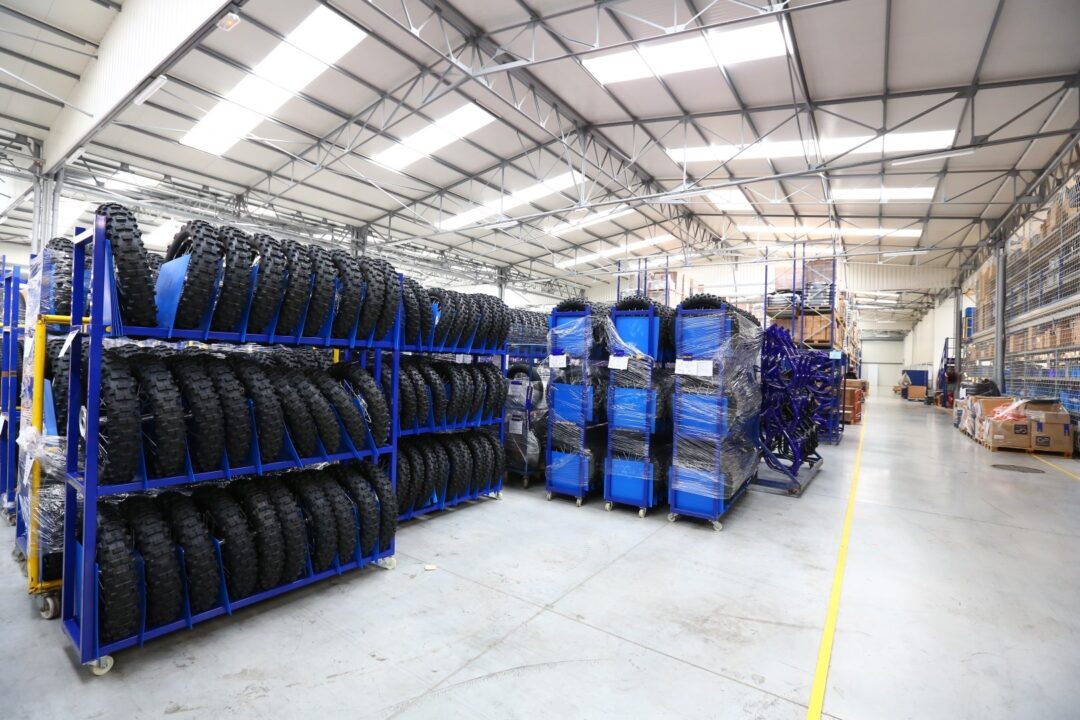
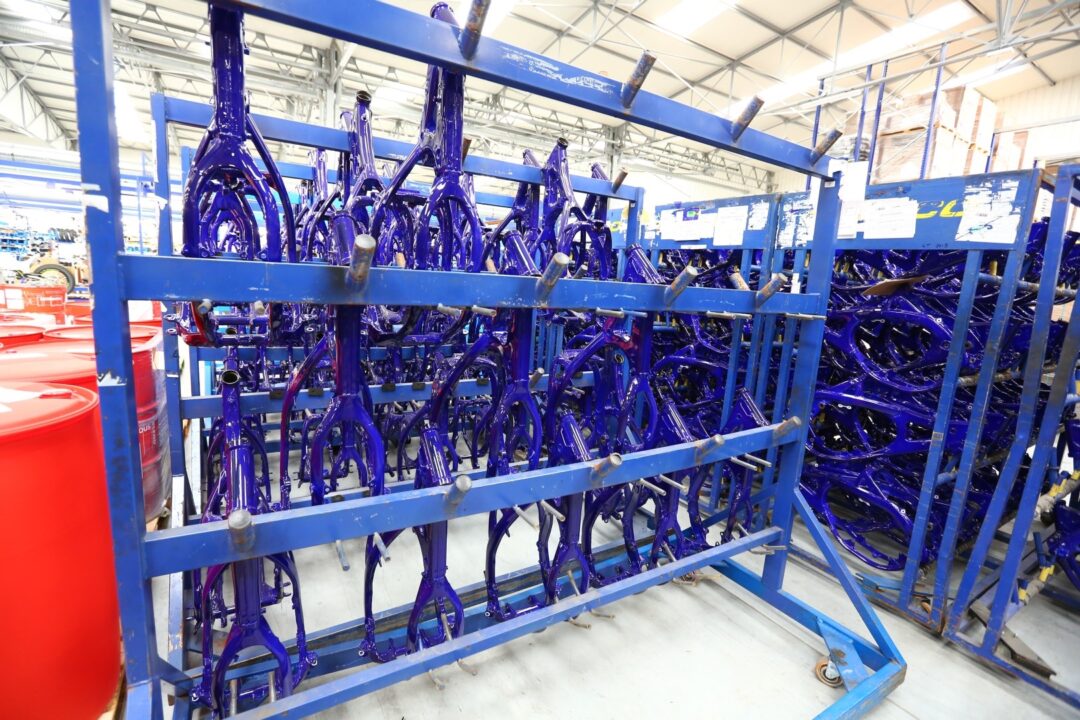
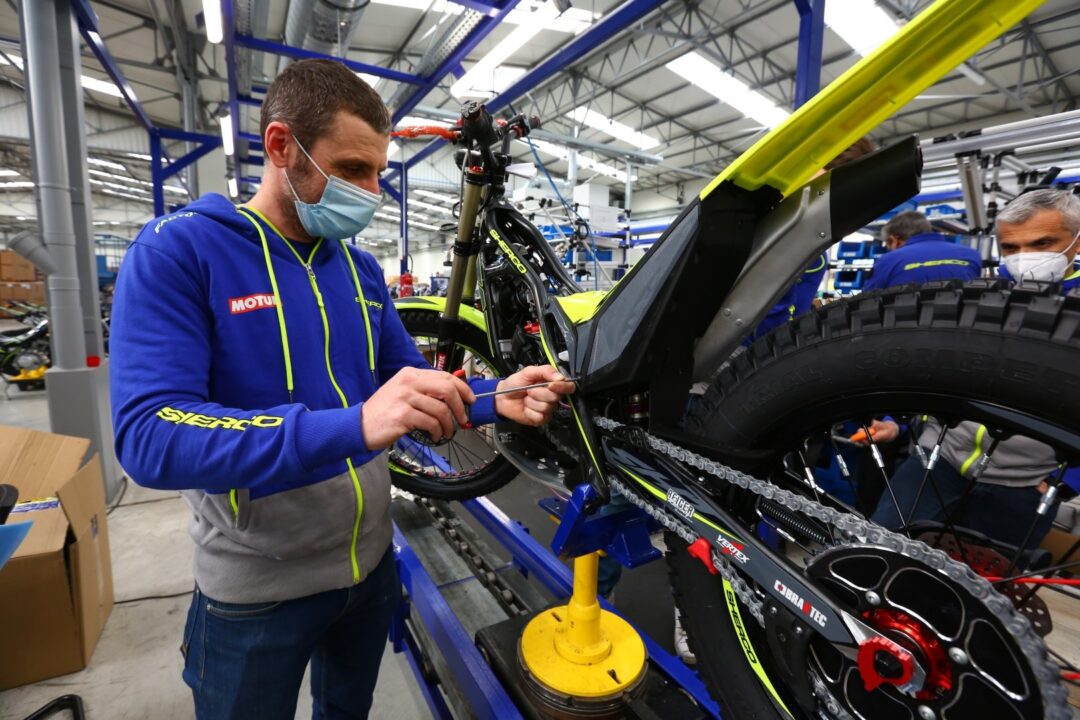
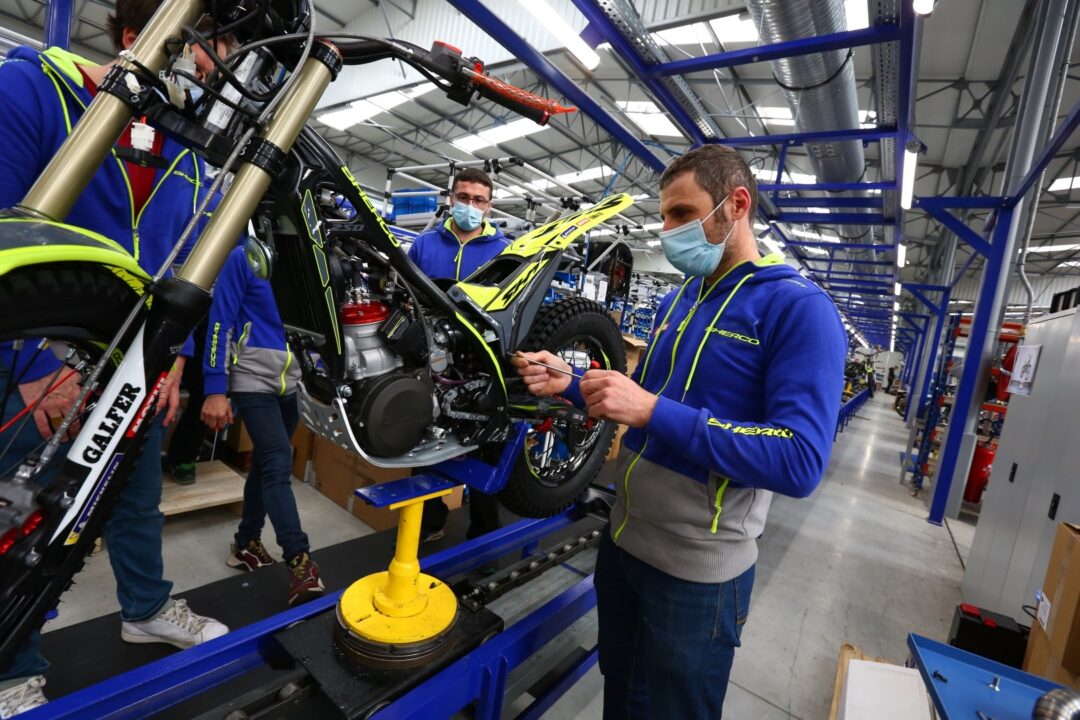
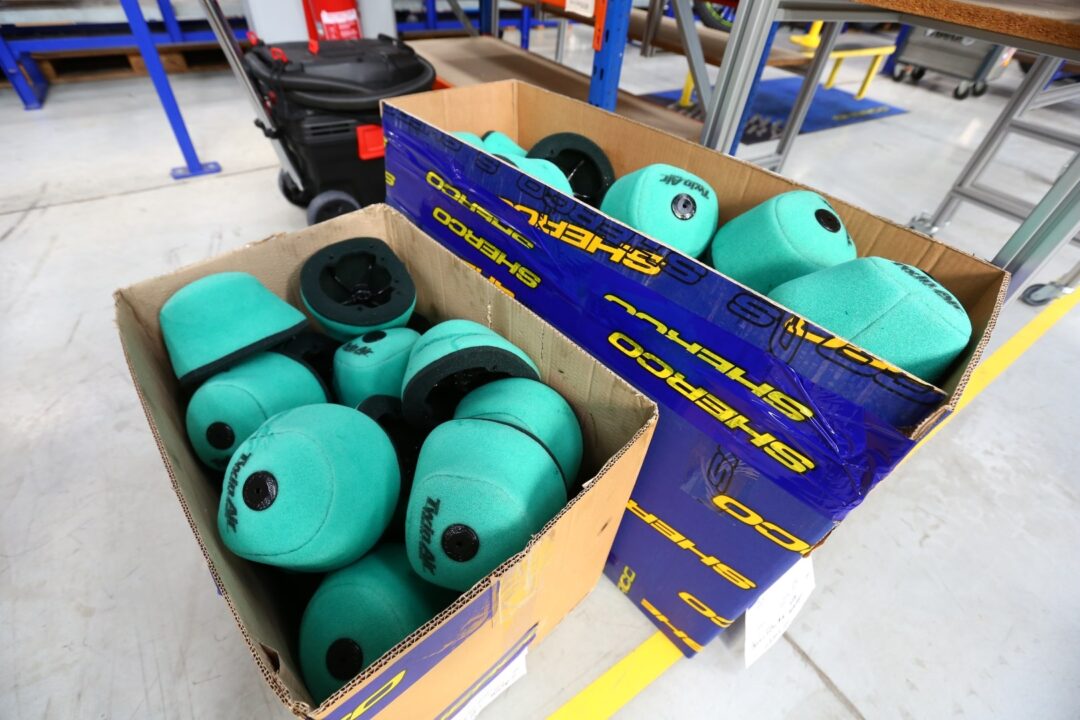
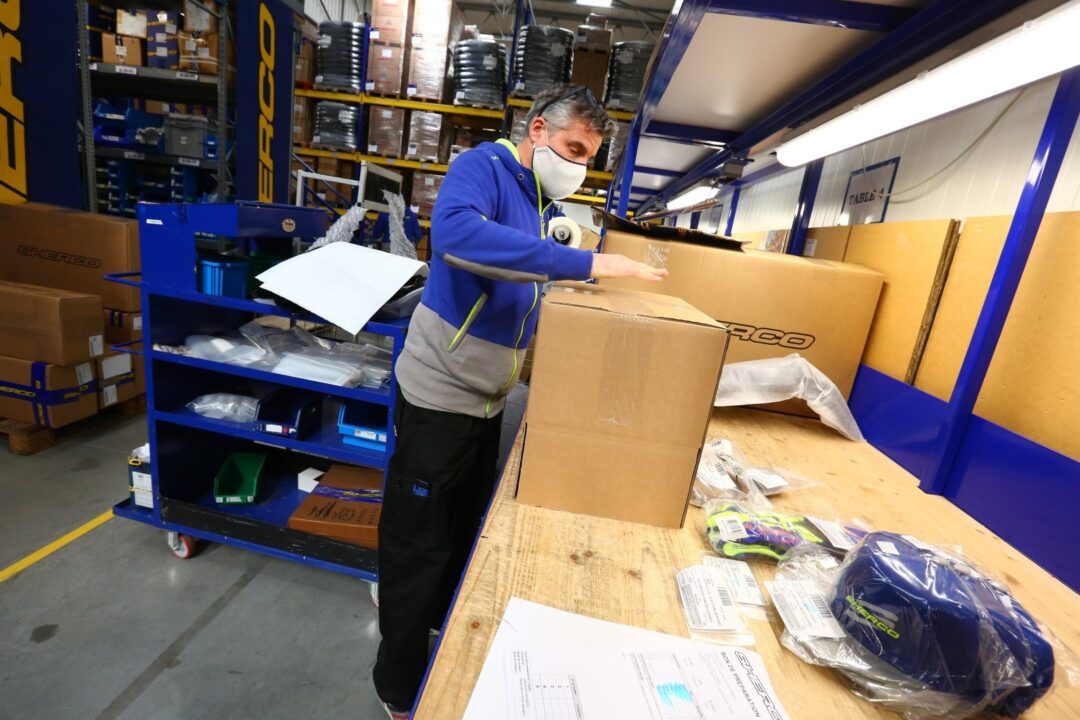
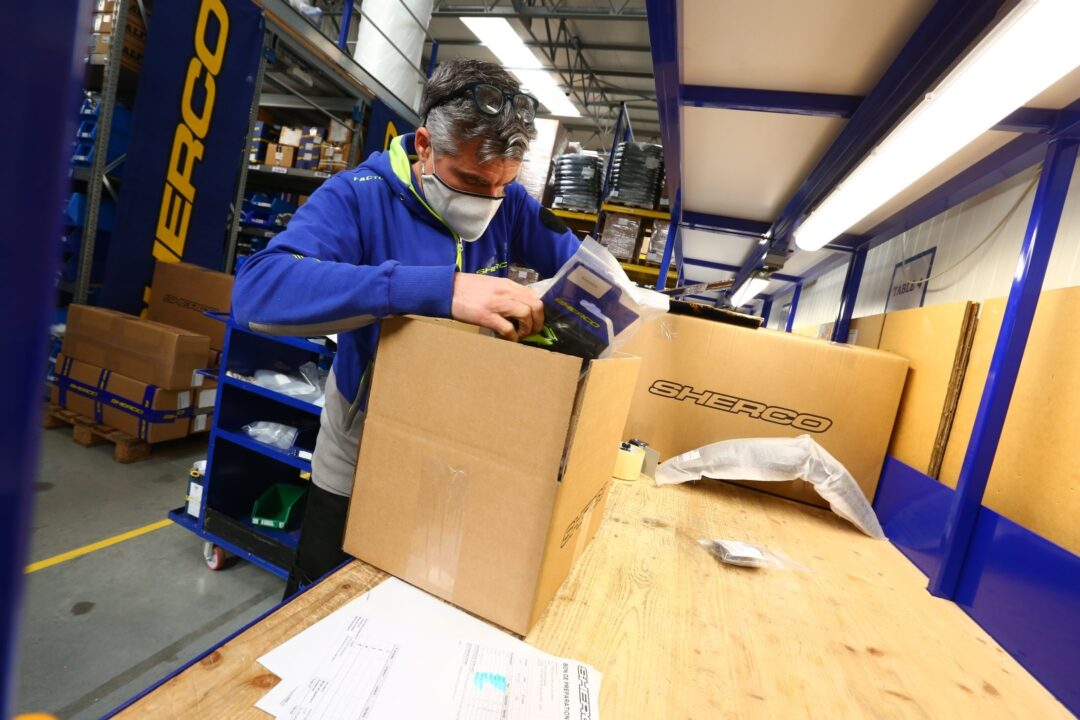
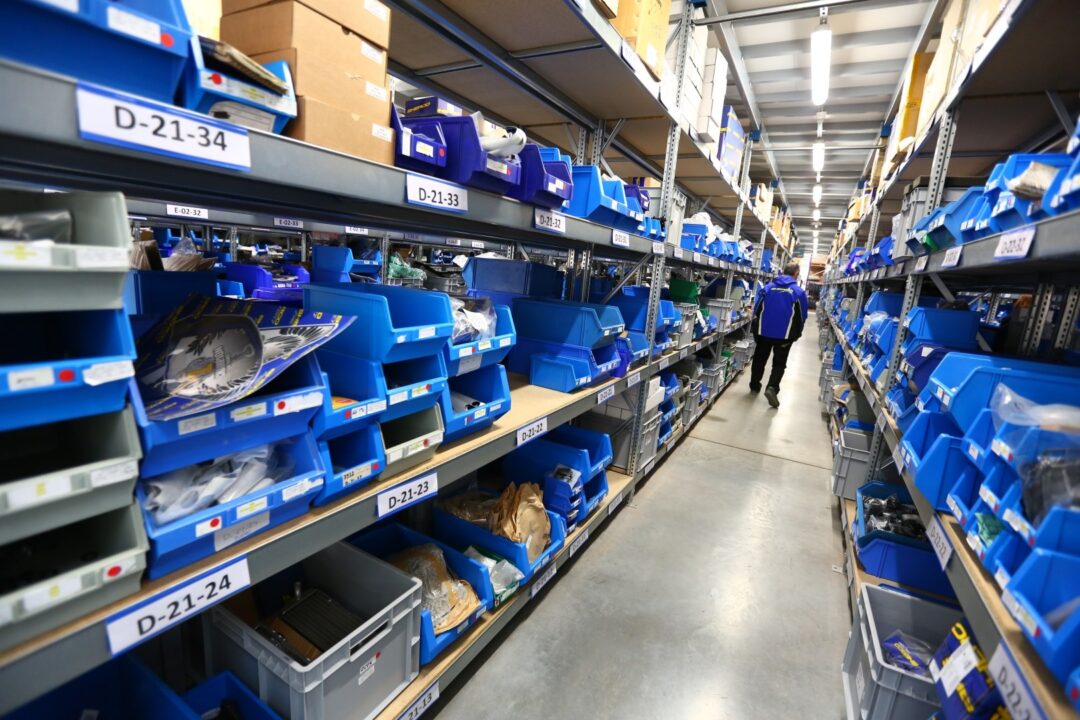

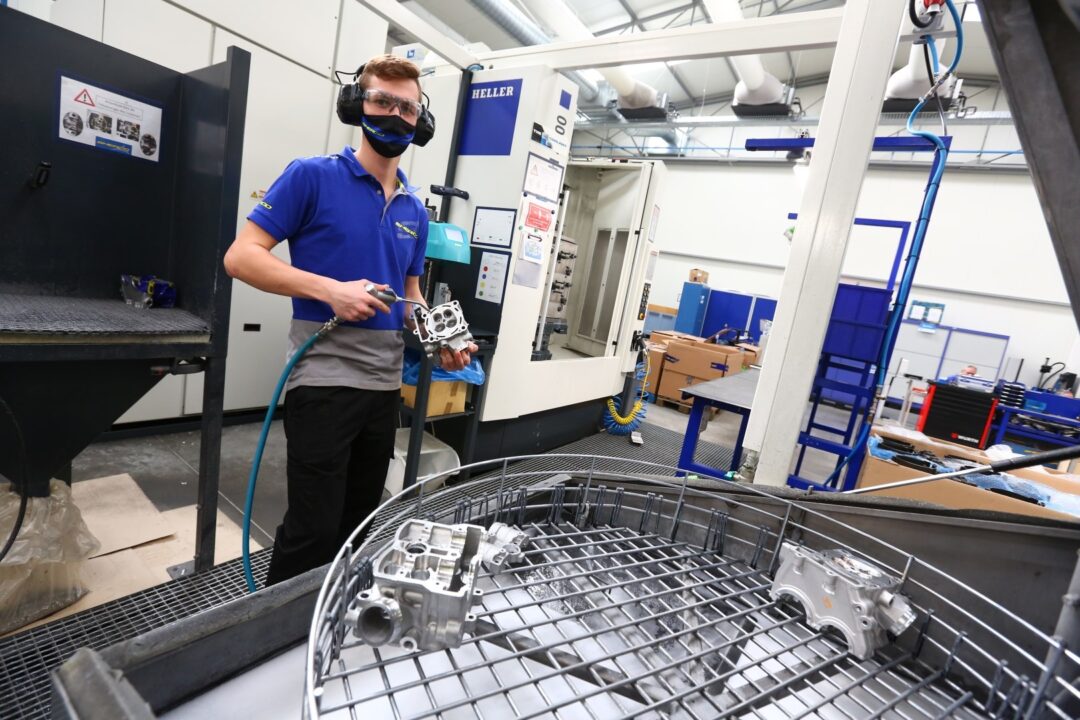
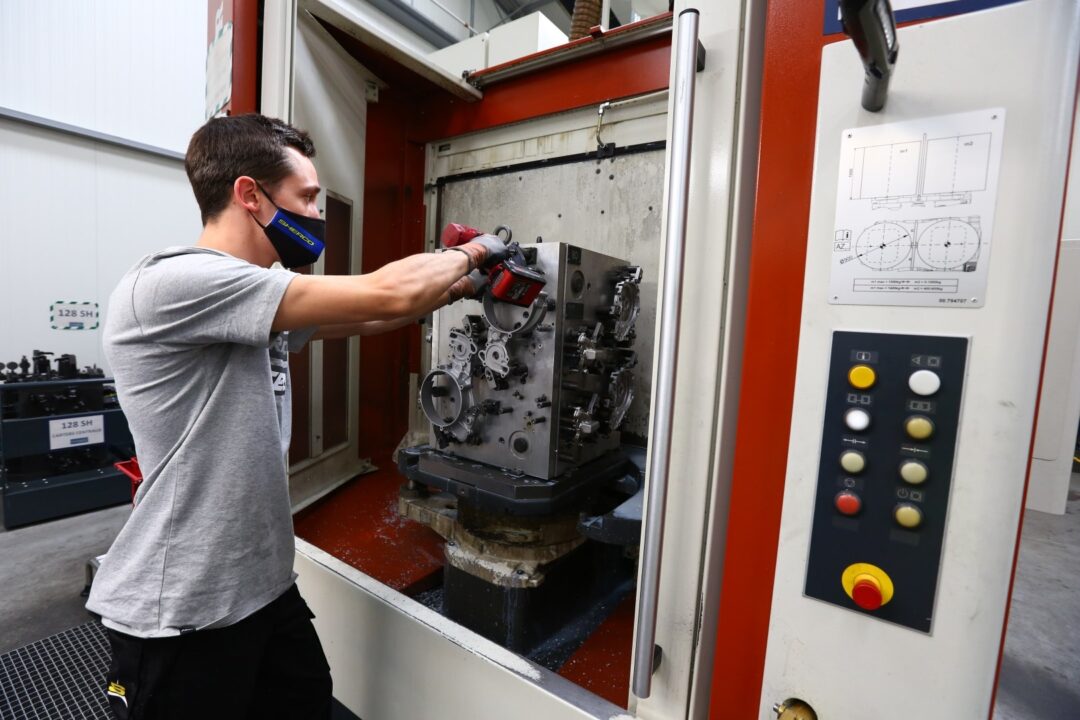
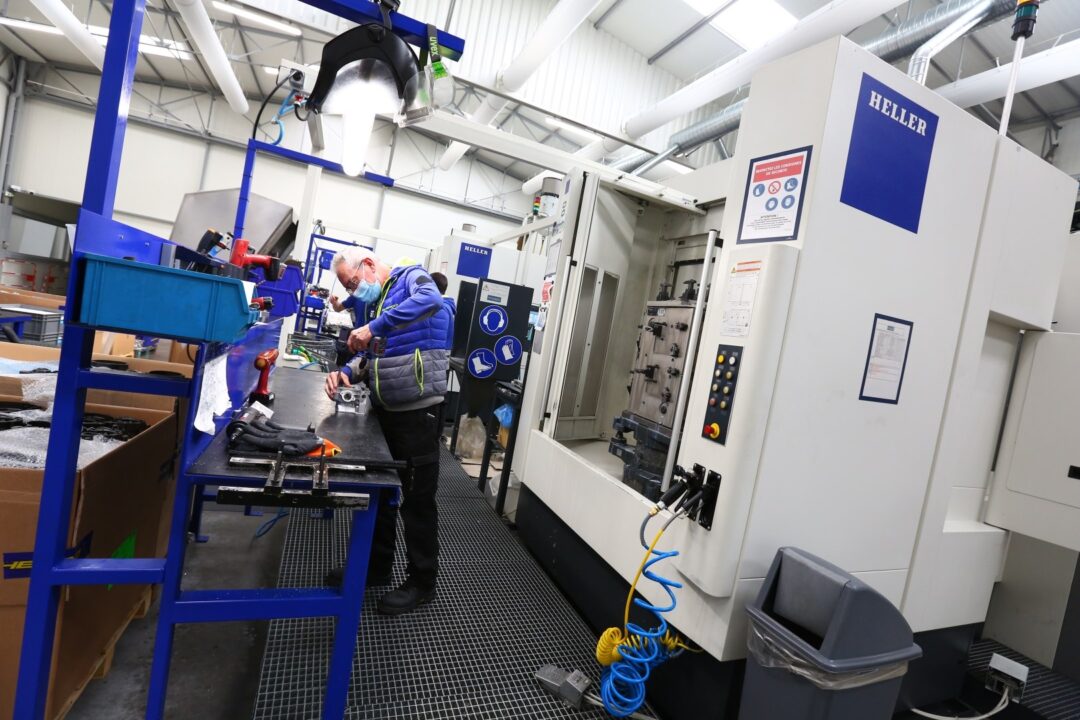
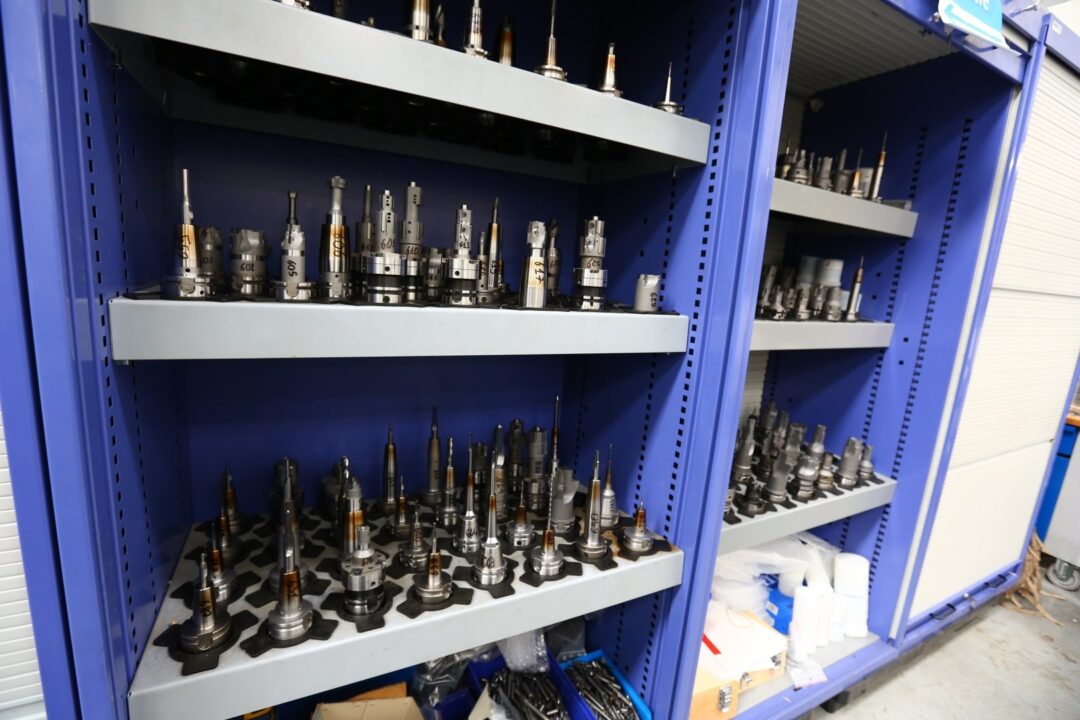


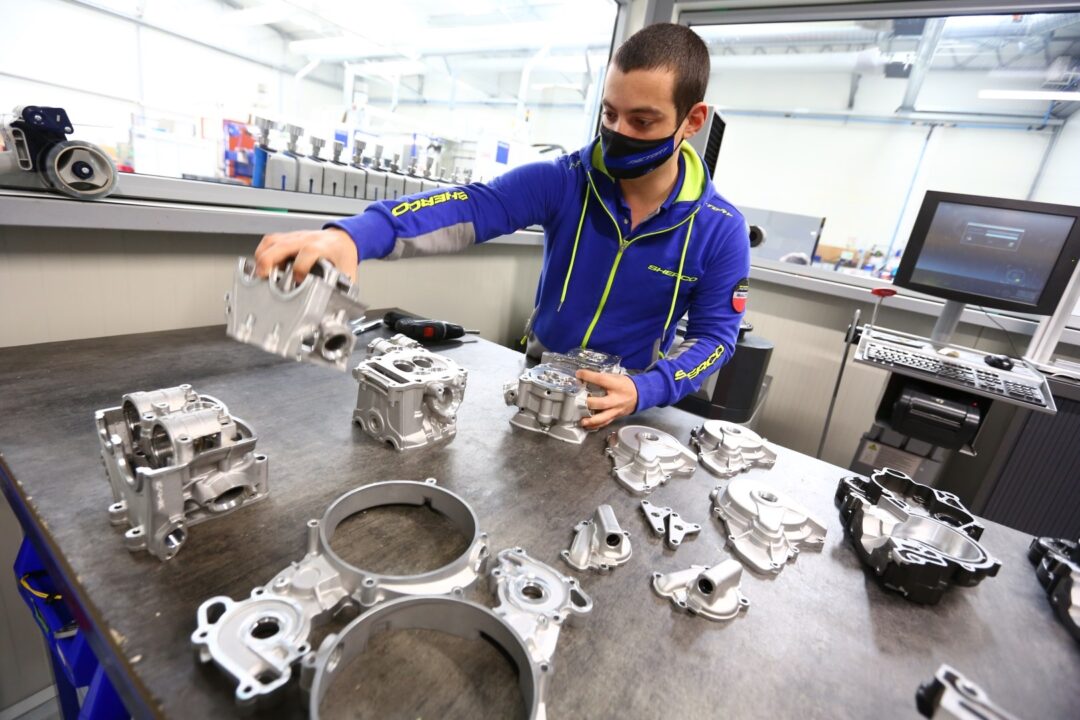
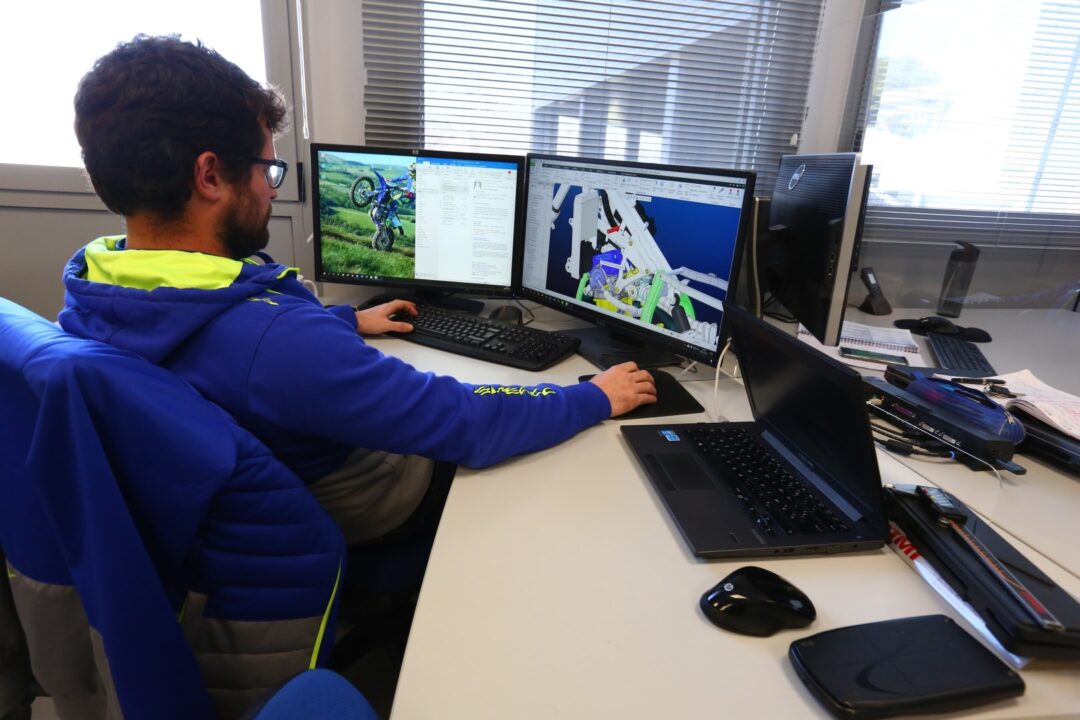
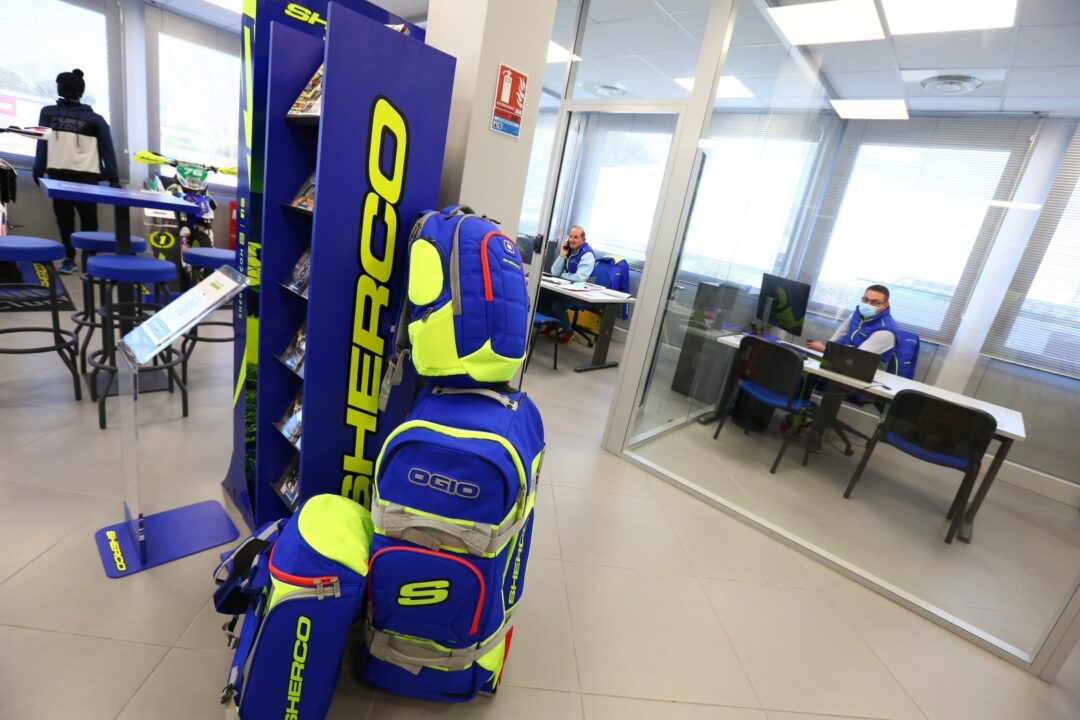
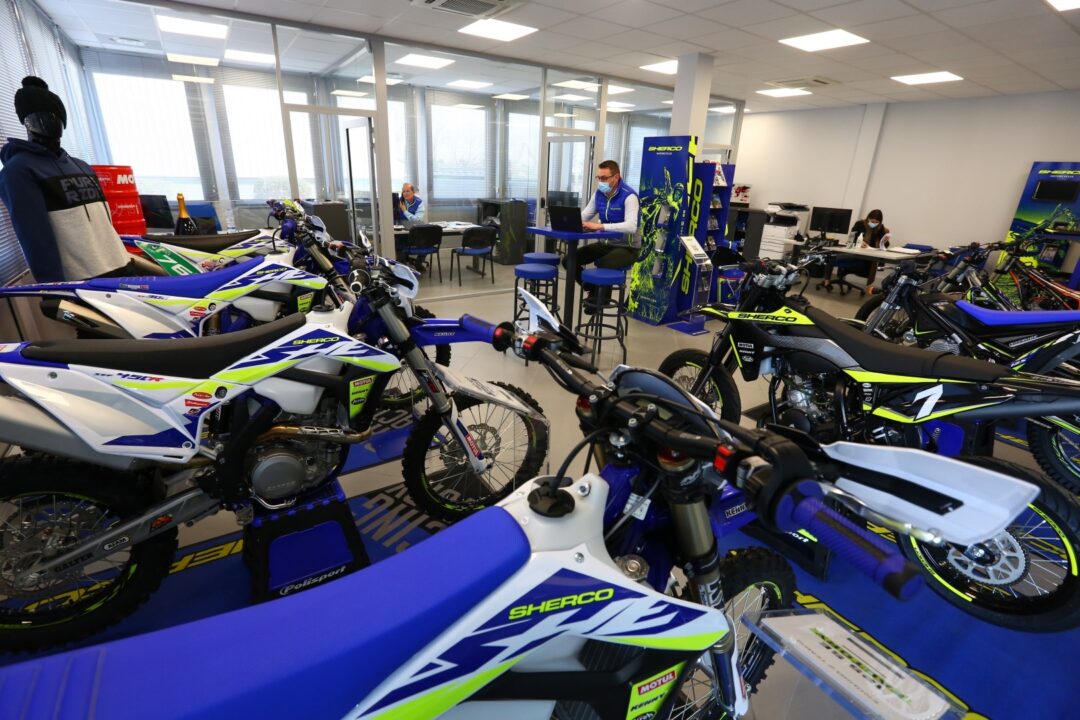
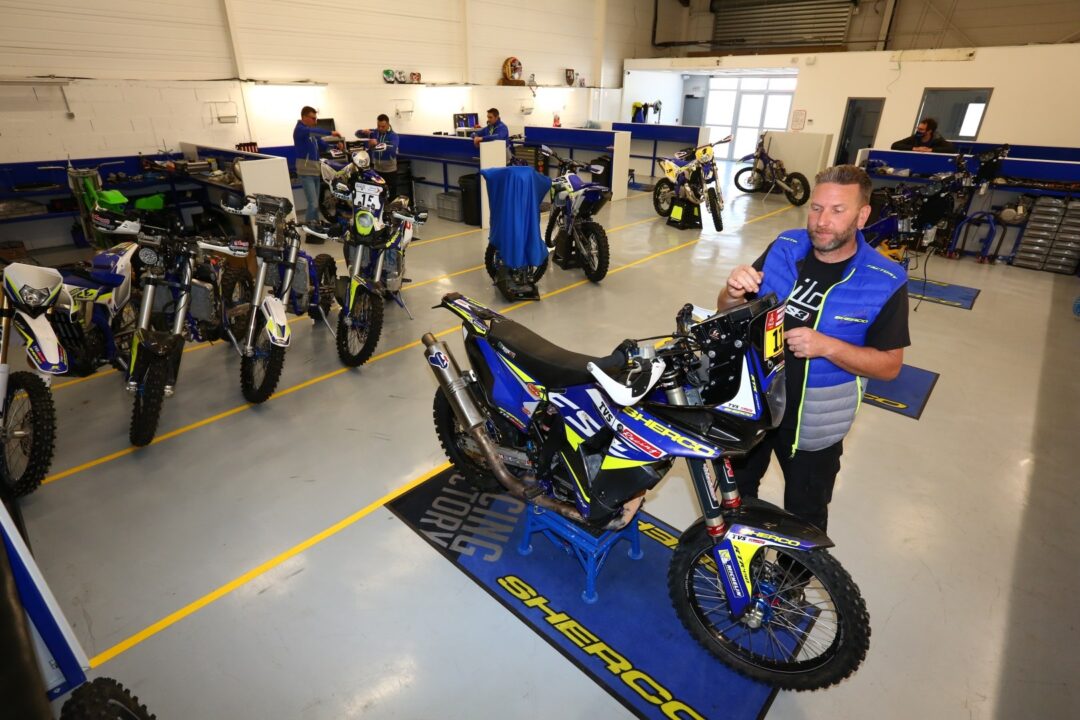
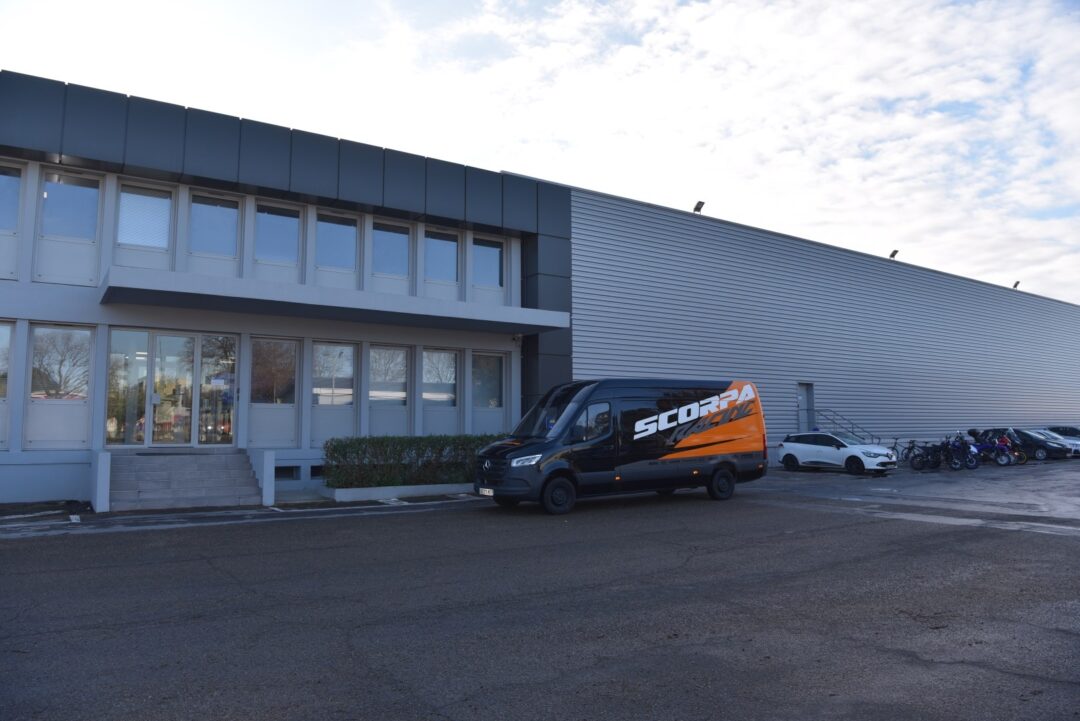
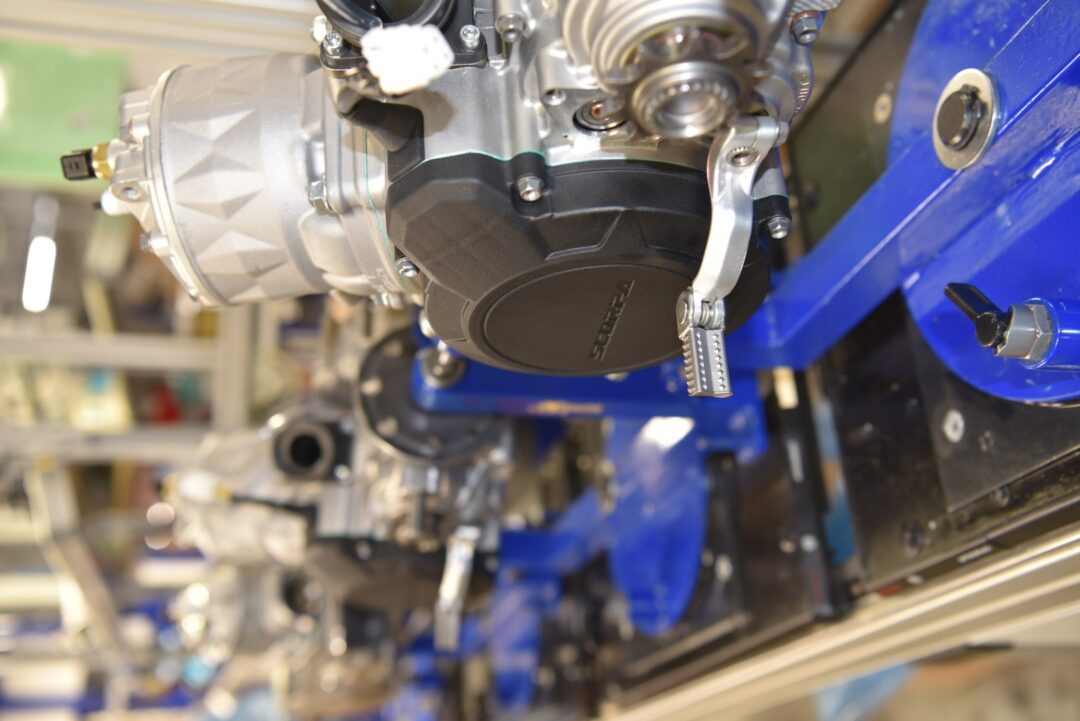
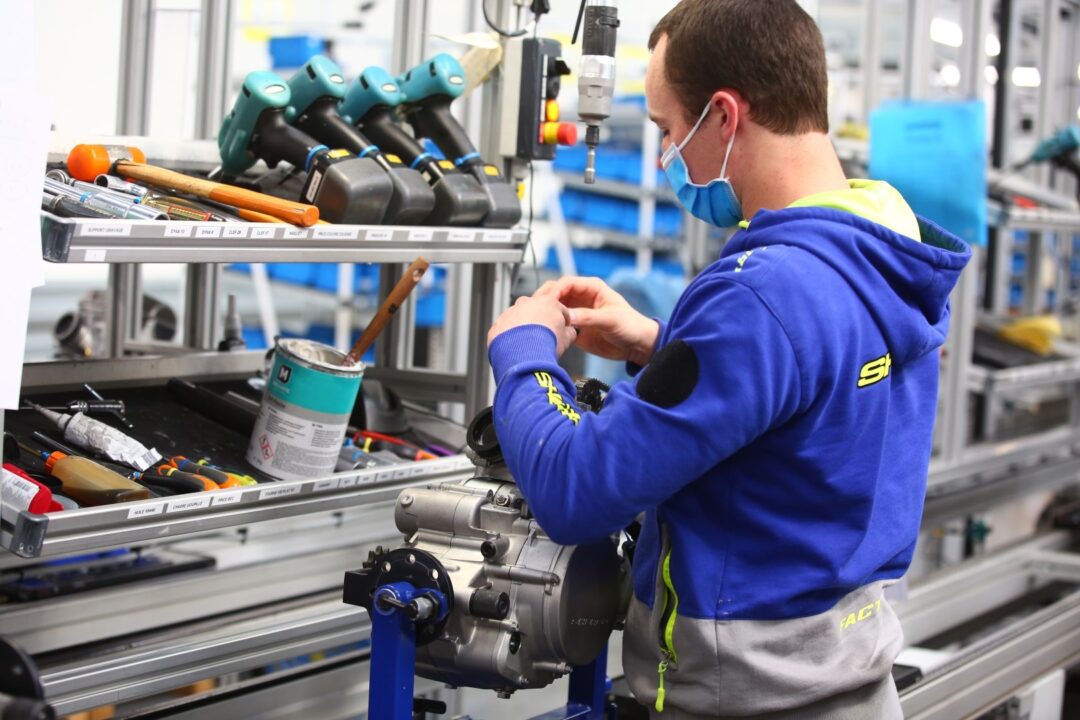
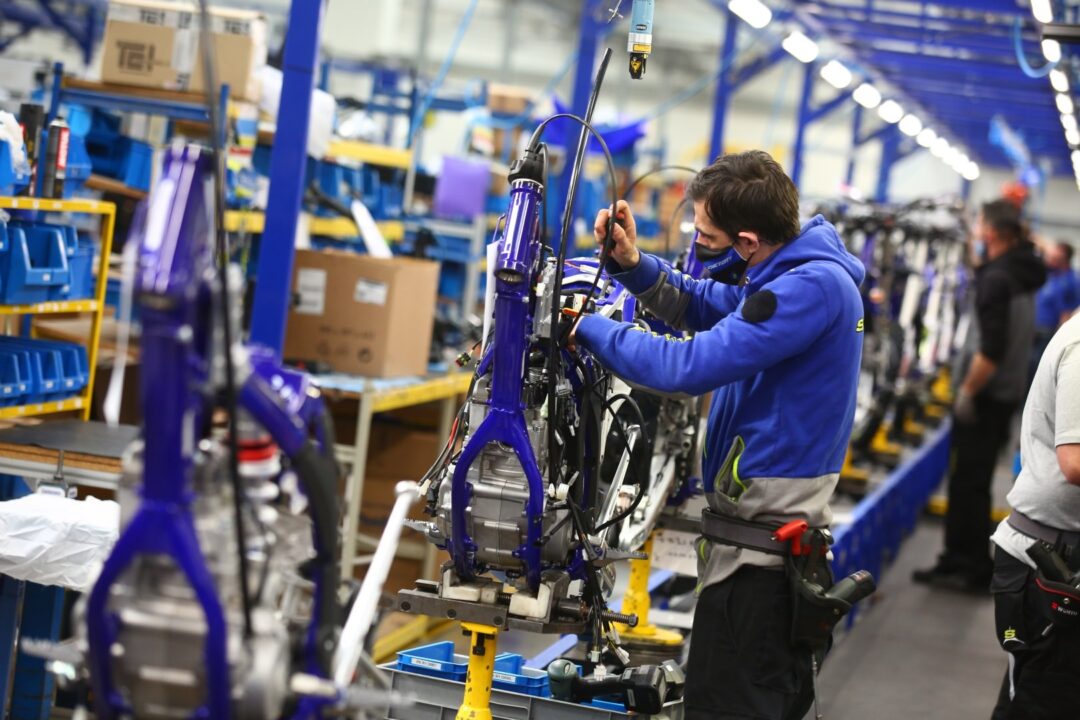
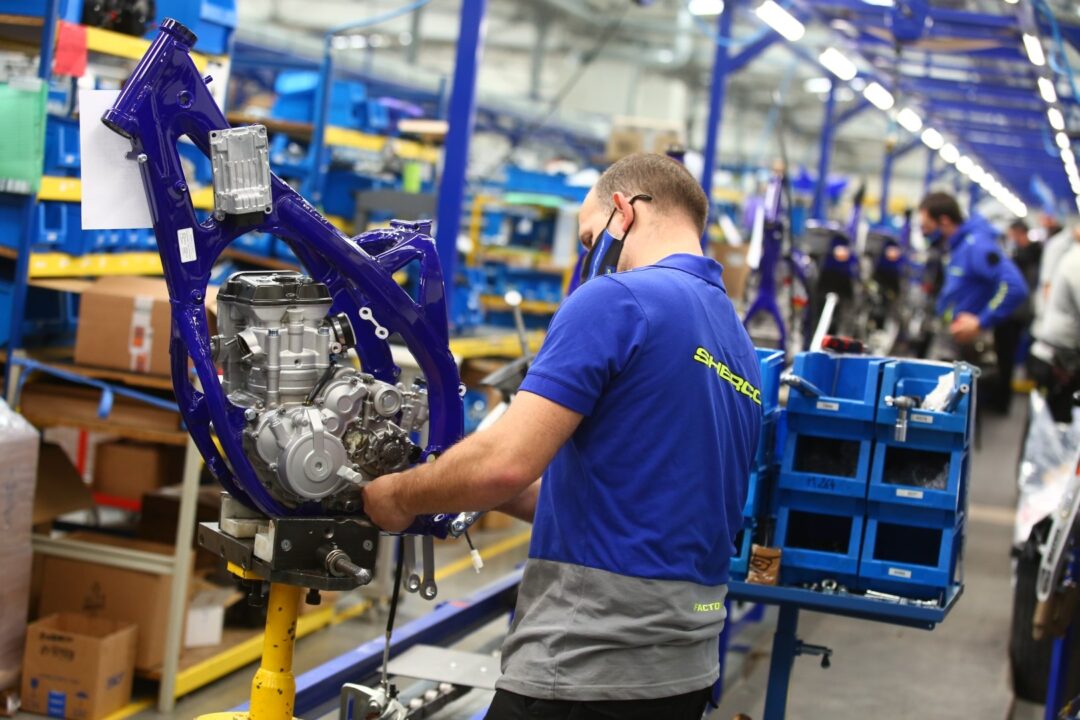
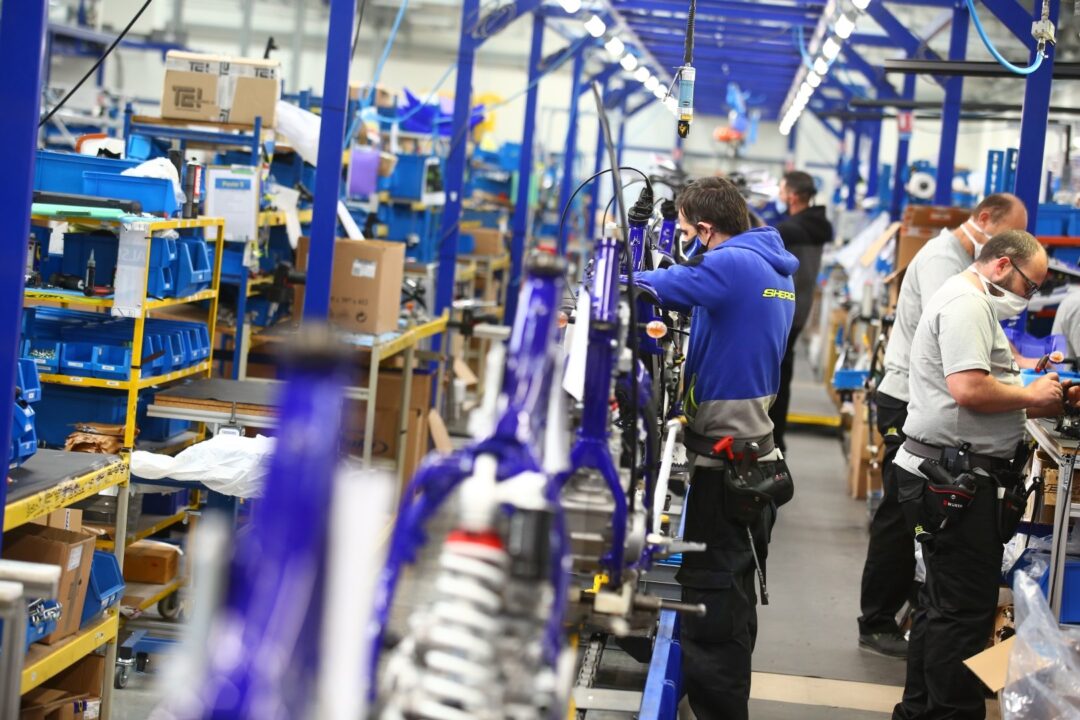
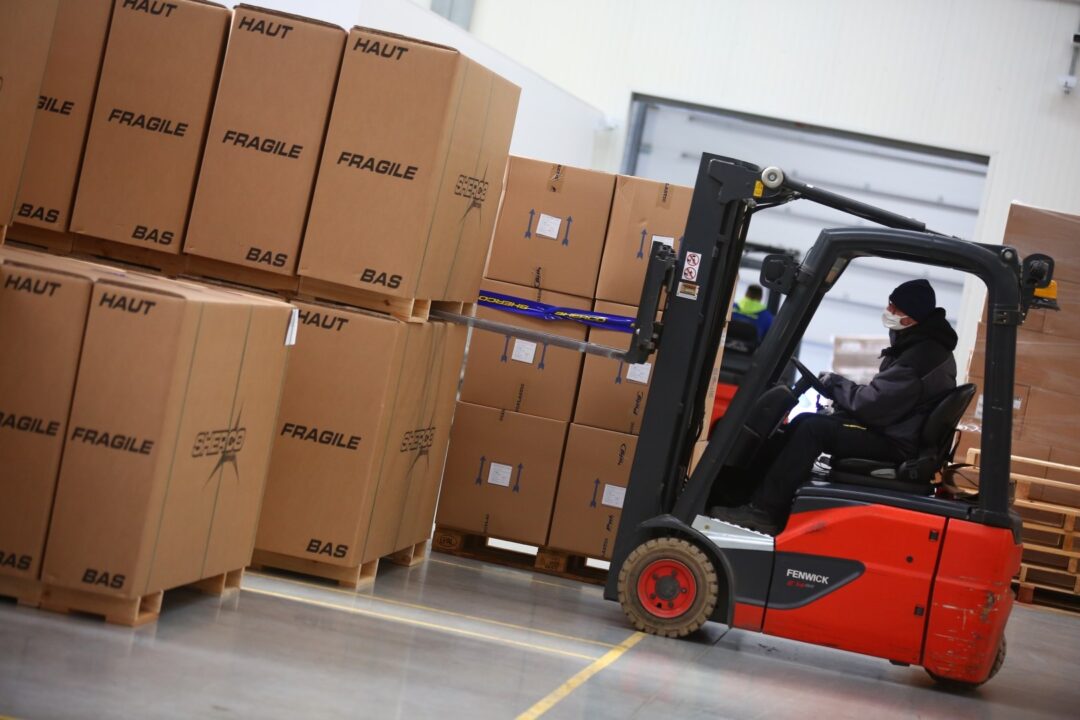
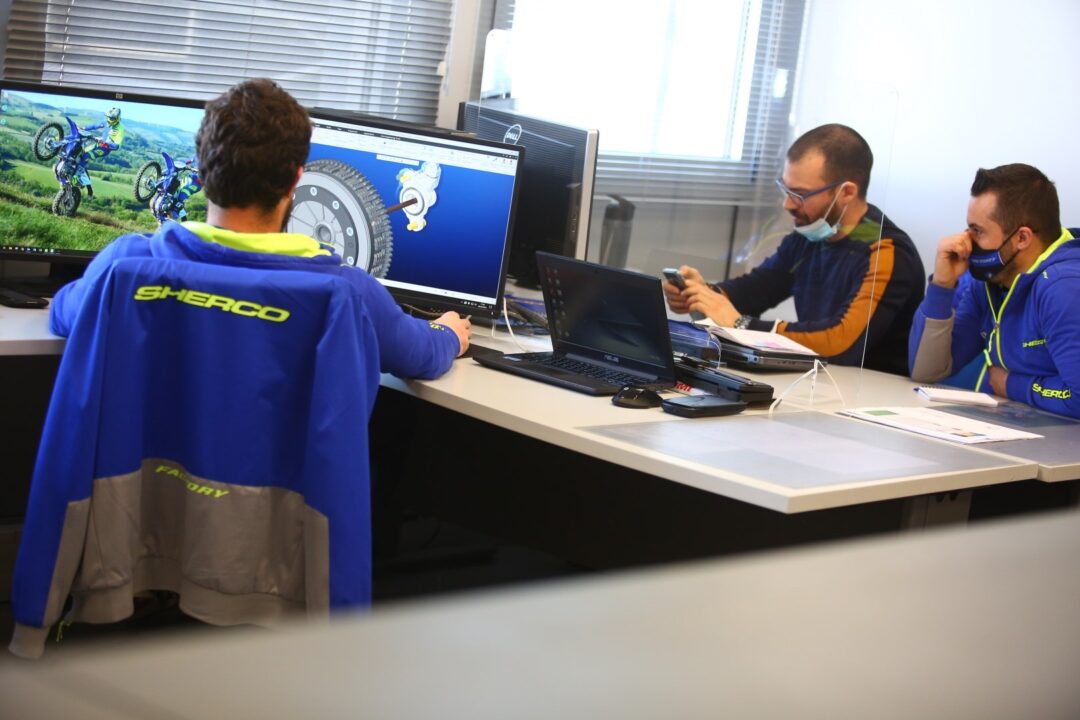